Facing the Decision
As the boat work continued, Monty became more convinced he wanted to sell the boat. Prior to his retirement, and buying the boat, we had been Whistler weekend warriors, driving up from the city on Friday afternoons and down very early on Monday mornings. During the pandemic, we were “stuck in Whistler“. It was not so bad! We golfed and biked in summer and skied in the winter. We could not travel, so it was nice to have these activities at our doorstep. Monty became accustomed to the Whistler lifestyle. He didn’t miss the boat upkeep. The boat was now fifteen years old. Despite all the maintenance we had done, there would be more. It was just a reality of boat ownership.
I had hoped he would change his mind so we could go cruising in the islands for at least one more season. During the pandemic, injuries kept me from skiing and golf for several weeks. I used that down time to prepare for our next sailing season. I passed an advanced drone pilot licensing course, got certified as a professional photographer, did a Marine First Aid course and took a writing course. Selling the boat meant setting aside some of my aspirations, particularly on the artistic side, in the short term. The sense of loss overwhelmed me, leaving me sobbing on Monty’s shoulder a few times. He kept telling me, “I am sorry!”
The final straw for me accepting Monty’s decision happened when a foot injury for inflamed again. Wearing deck shoes around the boat yard, instead of my runners with orthotics, had aggravated it. We were not getting any younger and our lifestyle at home was more active and healthier than the one we had on the boat. I faced the reality that it was better to let the boat go.
Maintenance Continues
Monty and I plowed on with the boat jobs. Trying to schedule skilled trades was sometimes frustrating. Everyone was busy trying to help the cruisers who had just returned from around the world. Priority was given to the boats heading offshore. Waiting on parts was another annoyance.
Monty and I agreed that if the boat didn’t sell, Whistler had to be ready to sail “offshore“. We would sail her to Fiji and try to sell her there. No corners could be cut (except for the countertop)!
The new Verona 4-burner stovetop we had brought with us from Canada as luggage was installed. The gas fitter came direct from his horse farm, leaving muddy tracks from his knee-high rubber boots on our back deck and cockpit. He didn’t seem to have a lot of experience with marine clientele. We had a boat builder cut a slightly bigger hole in the Corian countertop. The electric starter was wired but it meant turning on the inverter. In the end, using a barbecue lighter proved to be quicker. Here is a look at the new stovetop. It looked so shiny, we hesitated to use it!
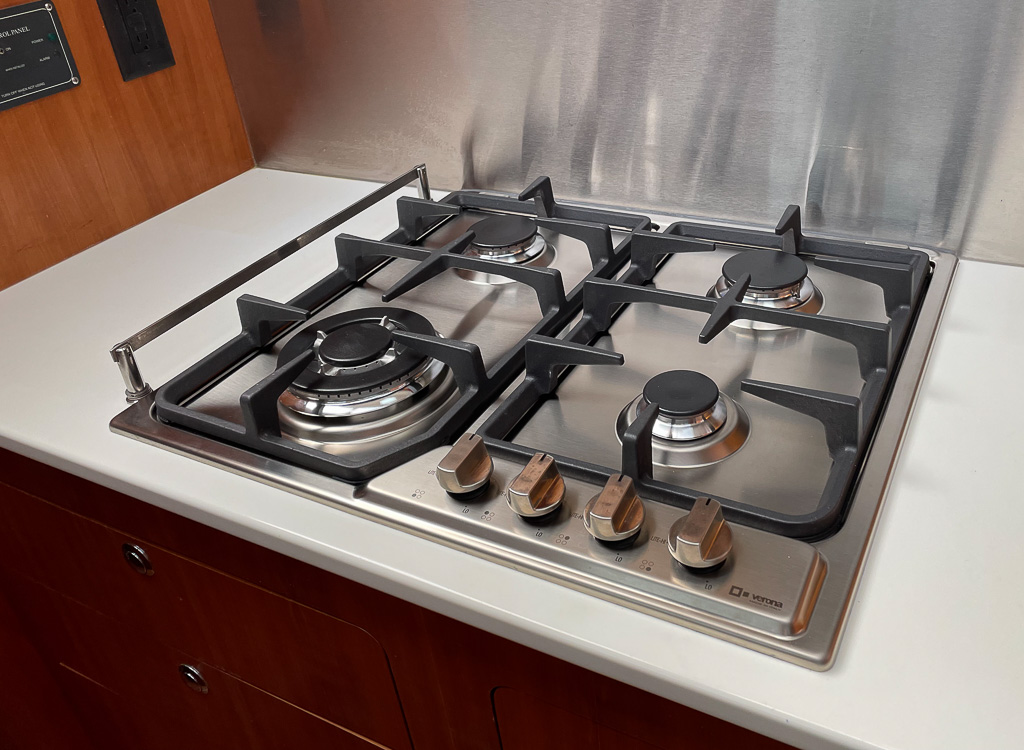
A problem with the inverter arose. Several long calls to Xantrex in Vancouver to try to get it working, an error code on the panel would not go away. The tech thought that the inverter had probably died. Monty pulled out the spare inverter (thanks, Christian for your foresight) from under the guest bed and was about to replace it. Monty tried resetting the inverter one more time and, Voila, the error code disappeared! A final call to a different support tech at Xantrex, and it was concluded the problem was “operator error“! One of the buttons had been on the wrong setting. Recalling how to operate all the boat systems, after a 30 month absence, was challenging. At least this blip ended well and didn’t cost anything other than our time!
While washing the decks, a couple of the deck hatches were found to be leaking. They had been re-bedded at Norsand Boatyard in 2017 but they didn’t do a good job! A few bolts were seized so we called TC Marine in to help. All the top-side hatches were again checked for leaks and the one over the battery locker also had a small leak, so it was added to the list. It was winter in NZ, so the work had to be done between frequent showers. Checking the MetService App for the weather forecast became almost an hourly habit.
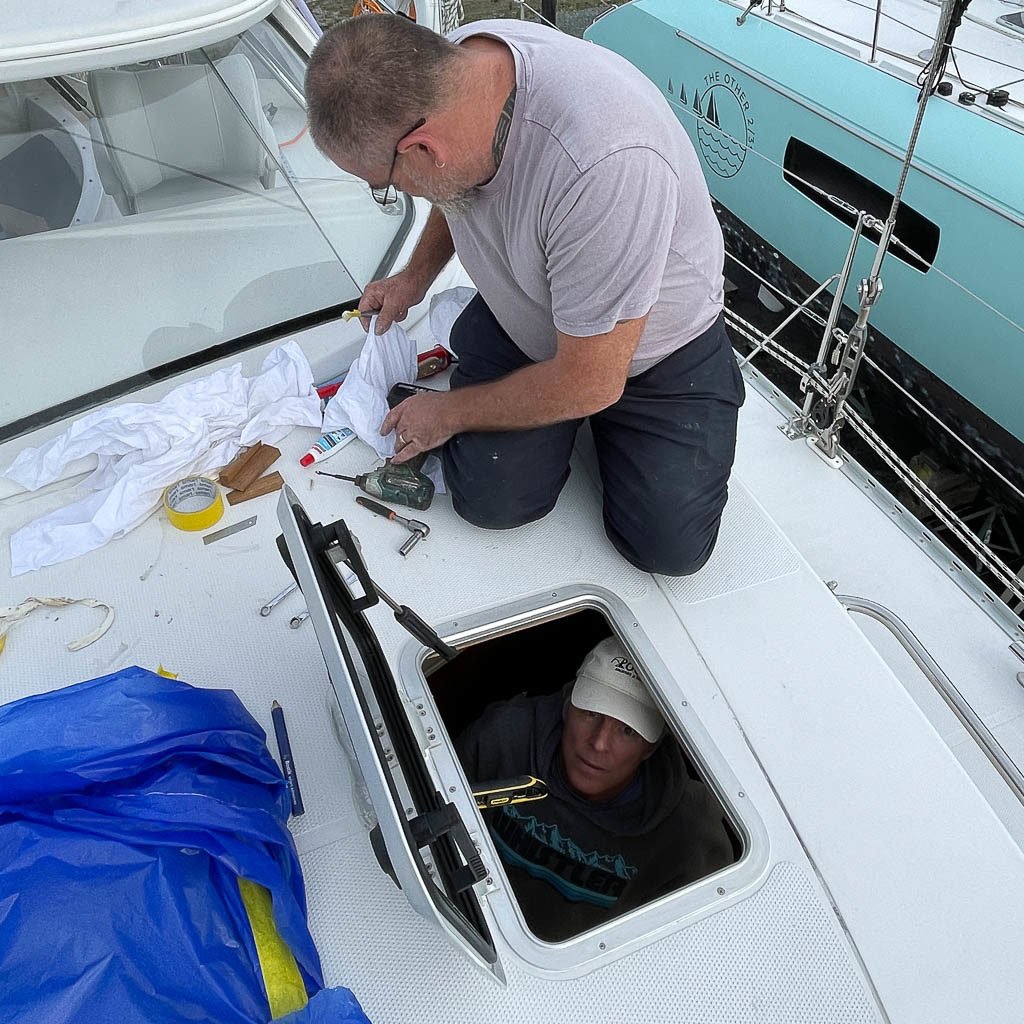
Monty and I replaced a couple of the sky screens. We cleaned and siliconed the others so the screens ran smoothly.
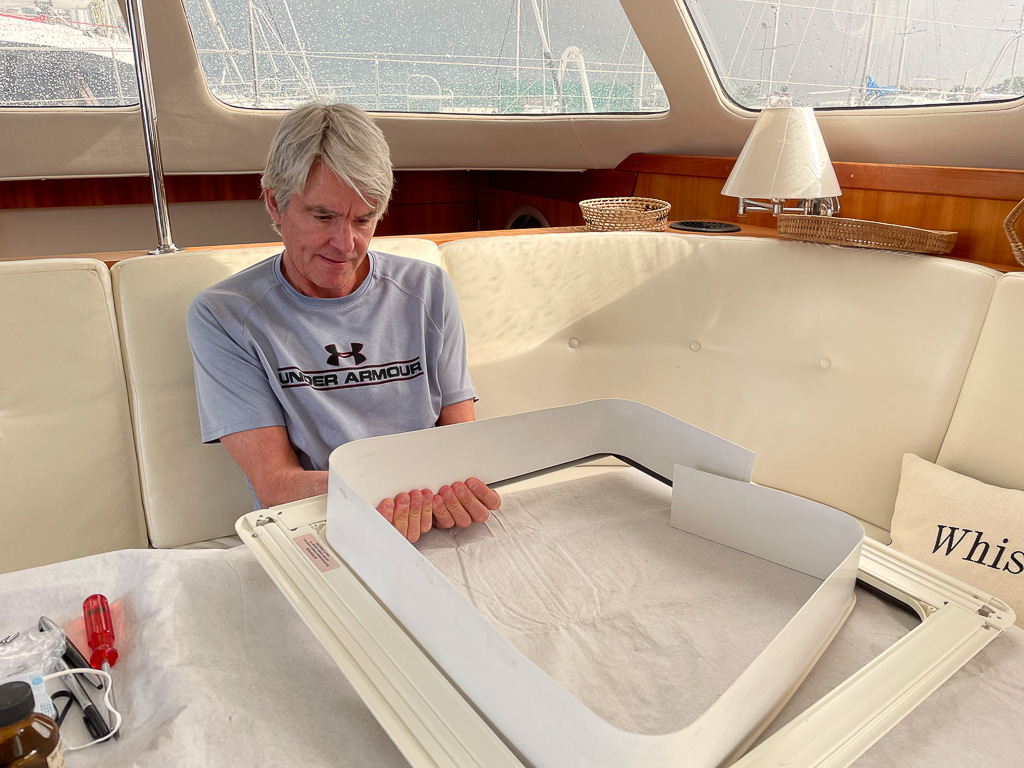
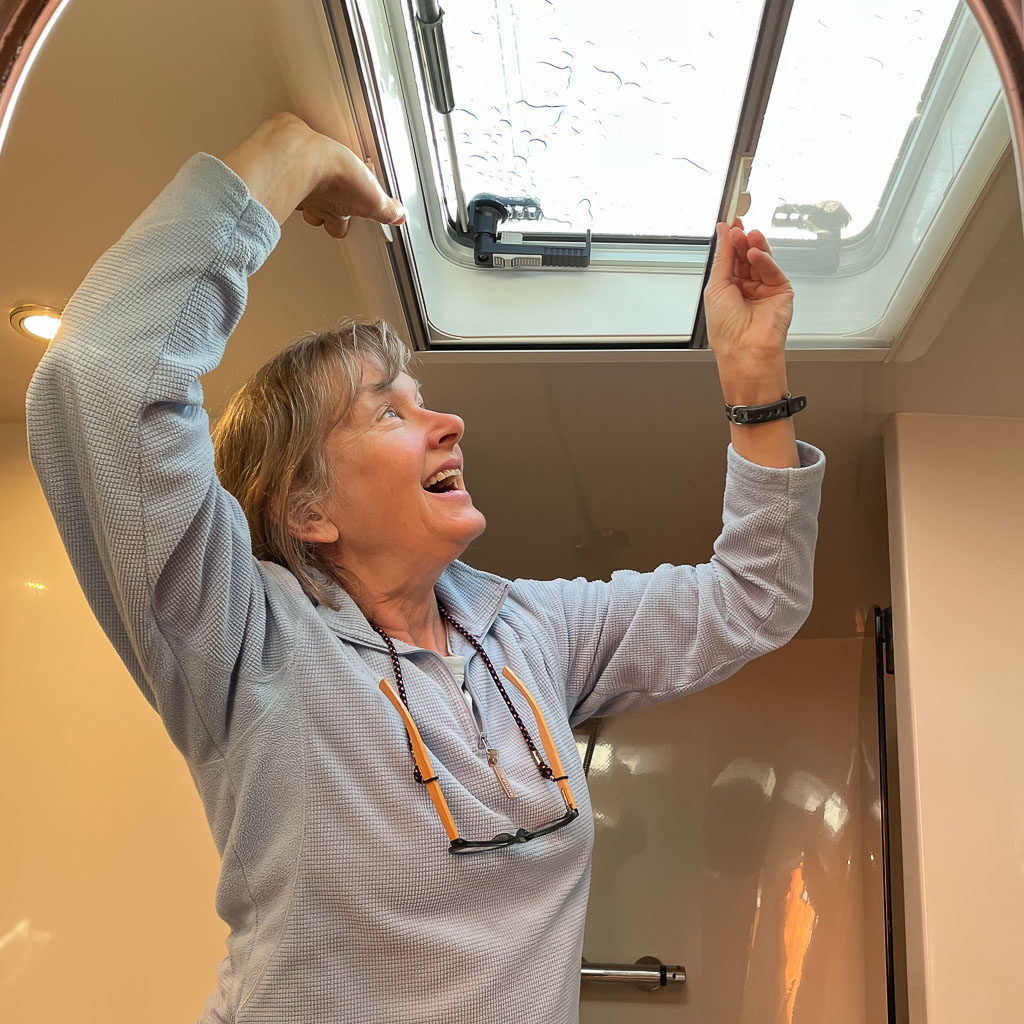
Our master head toilet was not flushing. The water in the bowl just went around and around. Monty tried to clear any blockage with vinegar. After a week without results, a plumber was brought in. He recommended replacing all the plumbing pipes from the toilets to the through-hulls. The toilet still wasn’t flushing so it was taken apart and some o-rings were replaced. After that, it leaked at the base. It was time to replace the toilets. Demand for toilets was backed up! We called around and managed to order the last two compact electric flush 12v toilets available in New Zealand. Once they arrived, we looked at them and thought they were smaller than the model we had. We were told that the model design had been altered in the last year and this was the way they were now. Monty and I pondered the size of the toilet once it was installed. The compact bowl was just too small!
We double checked the size of models online, measured and found our original toilets were regular, not compact! A mistake! We got back on the phone to the local distributor and were told there were no 12-volt regular size toilets in the country and a delivery was not expected until the end of June! It was currently the end of May. How could we wait a month for new toilets? With some negotiation and ingenuity from a staff member at the Whangarei office of Lusty & Blundell, they agreed to swap out a regular size bowl in a 24-volt toilet box for our compact bowl. It took a day or two but we managed to procure two regular size toilets! We never tested them out!
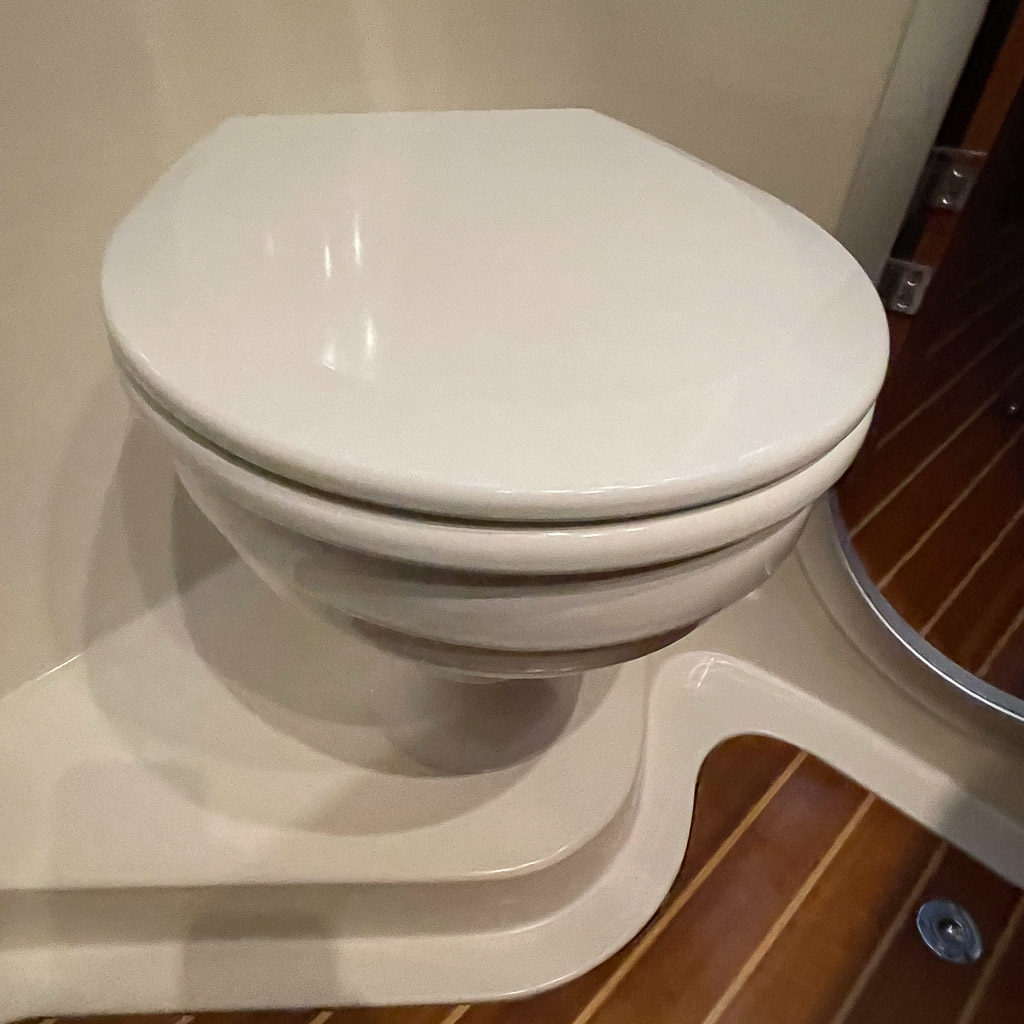
After the toilets were installed, the plumbing systems were checked for leaks. The port side was fine but not the starboard! A leak gushed from the through-hull after it had been dismantled and serviced. The boat couldn’t go in the water with a leak in the through-hull so our “splash” booking for that afternoon had to be postponed!
We had employed a boat builder company that we later found was in turmoil, trying to re-establish its presence in the boat yard. They couldn’t access trades to help us when we needed them. Communication was lacking. We ended up switching back to Trudy and her team at TC Marine who got on the jobs relatively promptly. We had been put off by TC Marine because every time we asked how long a project would take, they would say about 30 hours. In the end, we realized they were right. Certainly, changing the “poo pipes” did.
TC Marine’s plumber and very experienced boat builder, took the leaking through-hull apart and found the source of the leak.
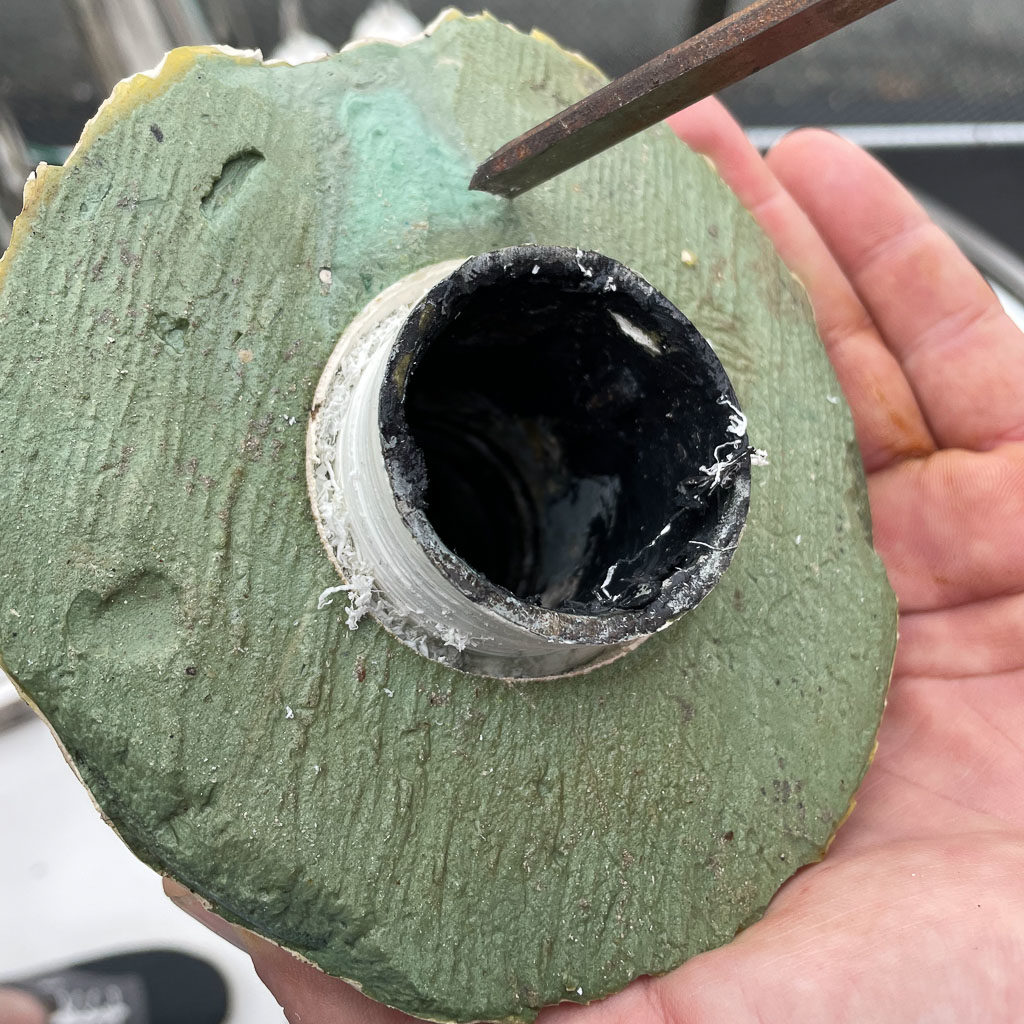
Joe replaced some parts with Tru-Design Ball Valve and cemented everything back together, fixing the leak.
We were about to schedule another launch when Monty noticed a crack in the fibreglass near the engine through-hull. Another gulp!
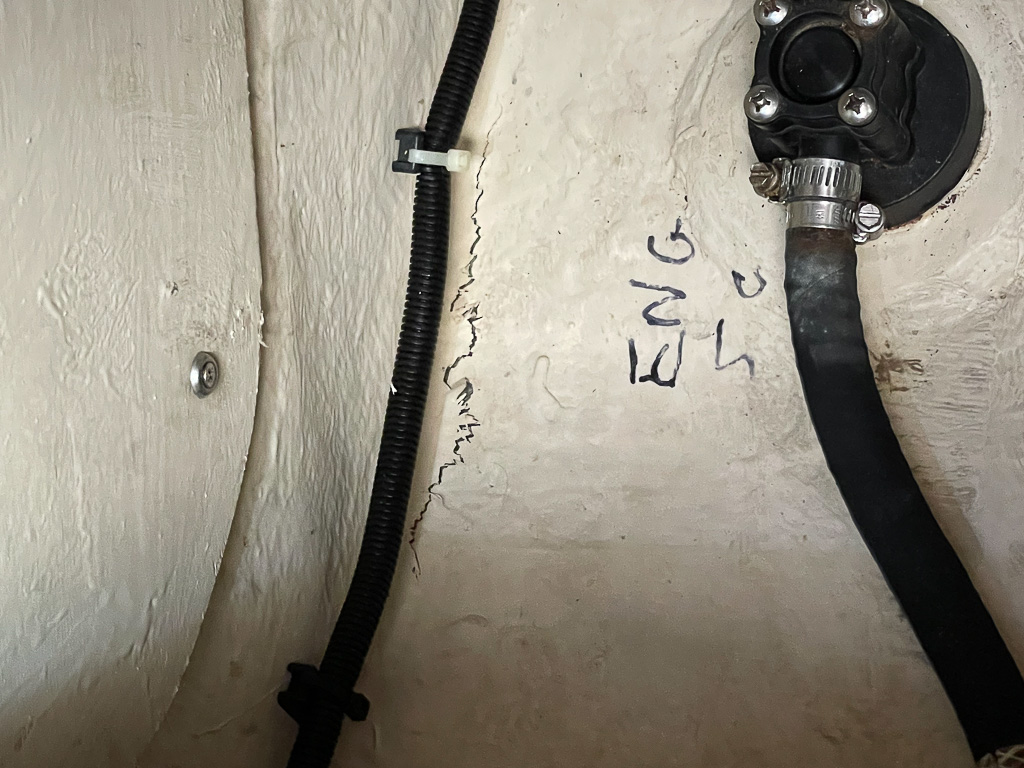
We rushed photos to our boat’s designer. He determined it is was just a crack in the taping. “Nothing to lose sleep over”, he said. We decided to delay the launch until the crack was repaired. Fixing the crack could have been done in the water, but it would have been taken more time (and money).
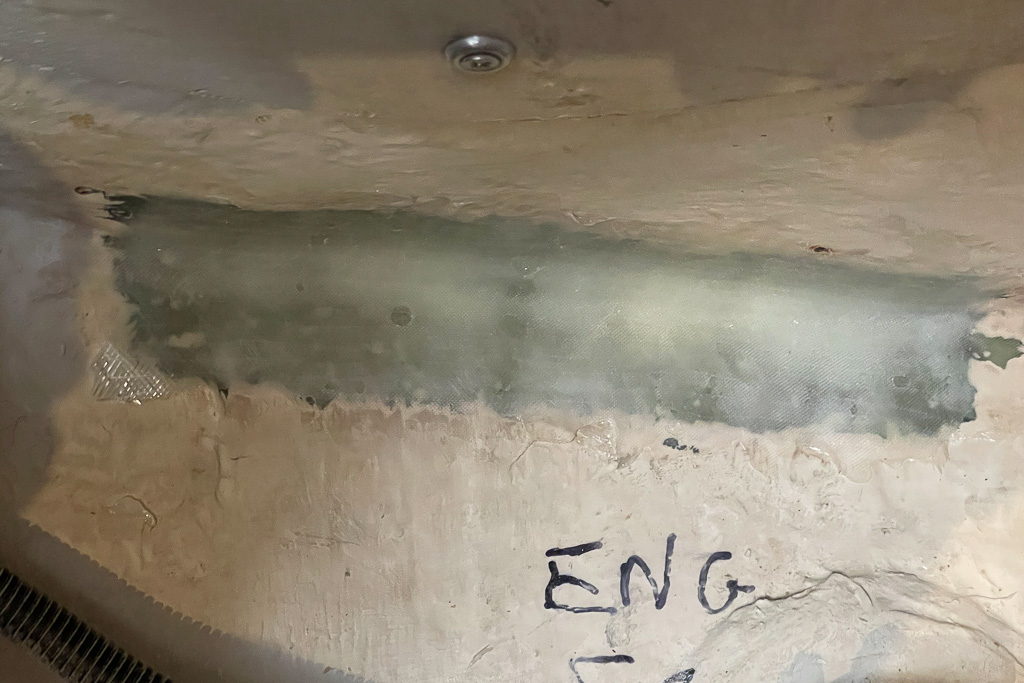
Four or five visits over a similar number of days and it was repaired. The final result was painted, not as shown above.
Monty had been trying to find the source of a small leak in the forward sail locker for a couple weeks. He finally figured out it was coming from the waste fitting. It was re-cemented to the deck with some Fix-15. Wonderful stuff!
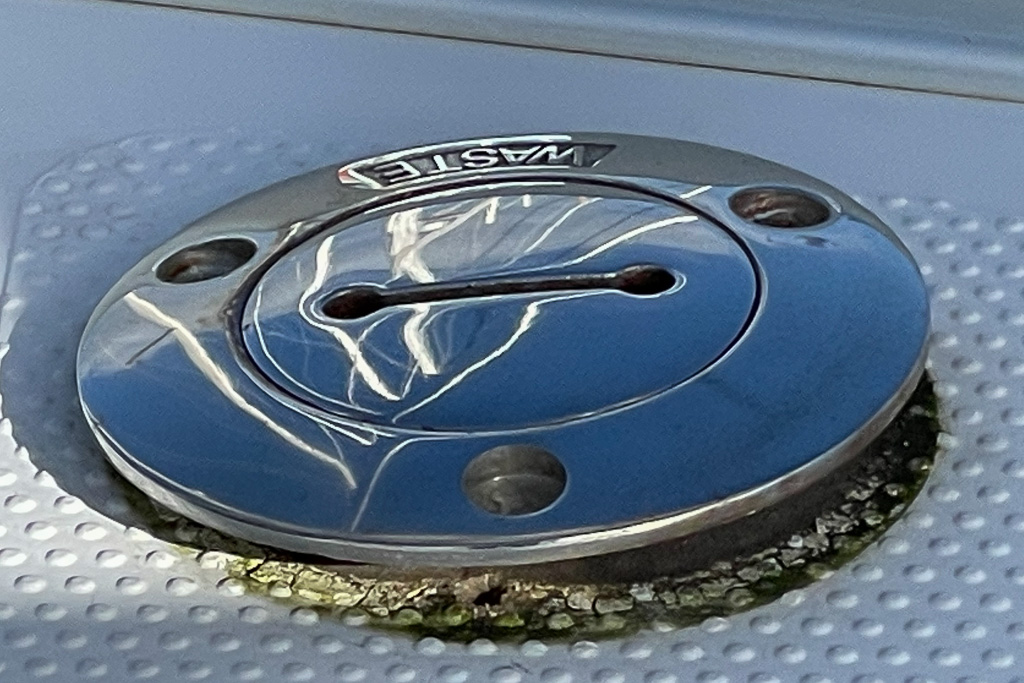
Before we had arrived in NZ, Hans Klomp, the Raymarine guy from Opua, installed some new electronics. Two new Axiom Pro chart plotters (warranty replacements for our E127s plotters that had acted up on our last passage to NZ), two i70s display instruments, a new maintenance-free Airmar Ultrasonic Speedo and a few other backbone components were installed. He ran the cable for the speedo part of the way but ran out of time. Getting the high speed cable with its special connectors the rest of the way proved challenging. The cable had to be pulled through a small new opening in bulkhead, behind the oven and around some partitions. Monty got it done. Hans drove 2 hours back down from Opua and finished the installation of the Airmar box and wiring. He ensured us he could do it quicker and cheaper than employing someone locally as he had all the parts and cables in his van and knew the boat.
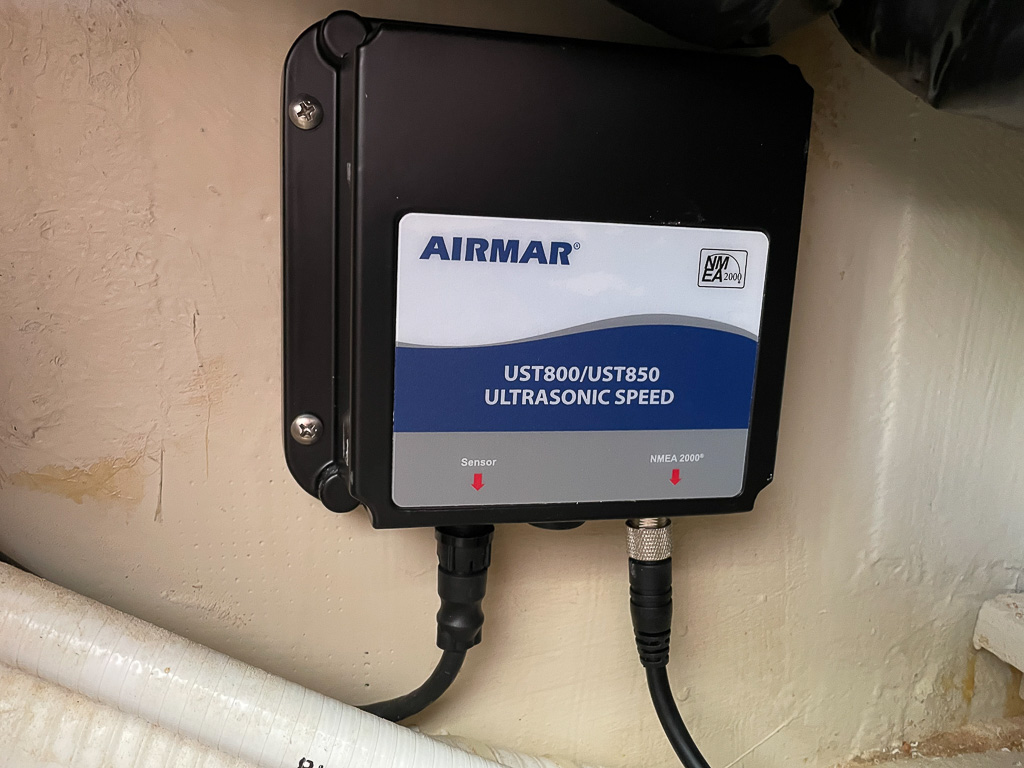
Hans Klomp sits at our helm. He has been a great resource over the last several years, providing excellent advice and support for our electronics. He also kept us informed on relevant news and possible New Zealand border opening dates during the 2-year lockdown.
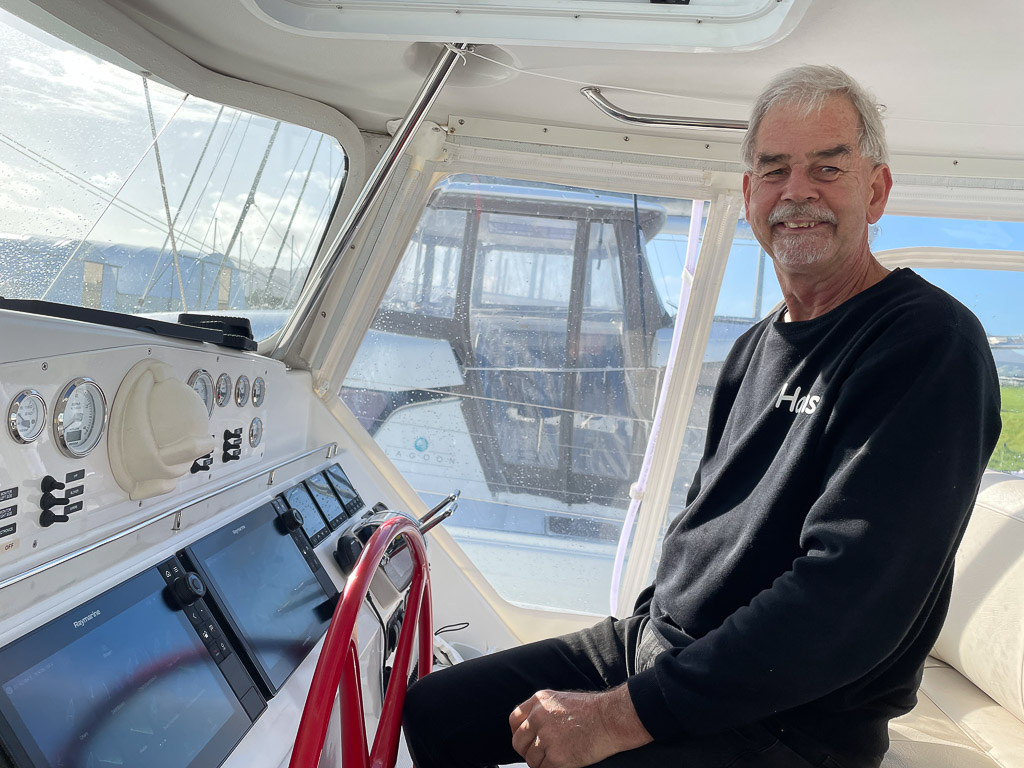
In fall of 2019, we had contracted Canvas & Covers to make a new cockpit enclosure which was completed before COVID really got going in early 2020. When we arrived, the enclosure didn’t fit properly and there were numerous deficiencies. It was a bit surprising since the same canvas maker had made the previous enclosure. After several visits over a two month period, some panels were completely redesigned and adjustments incorporated. The new enclosure was very functional and looked great. Brendan ensured we were happy.
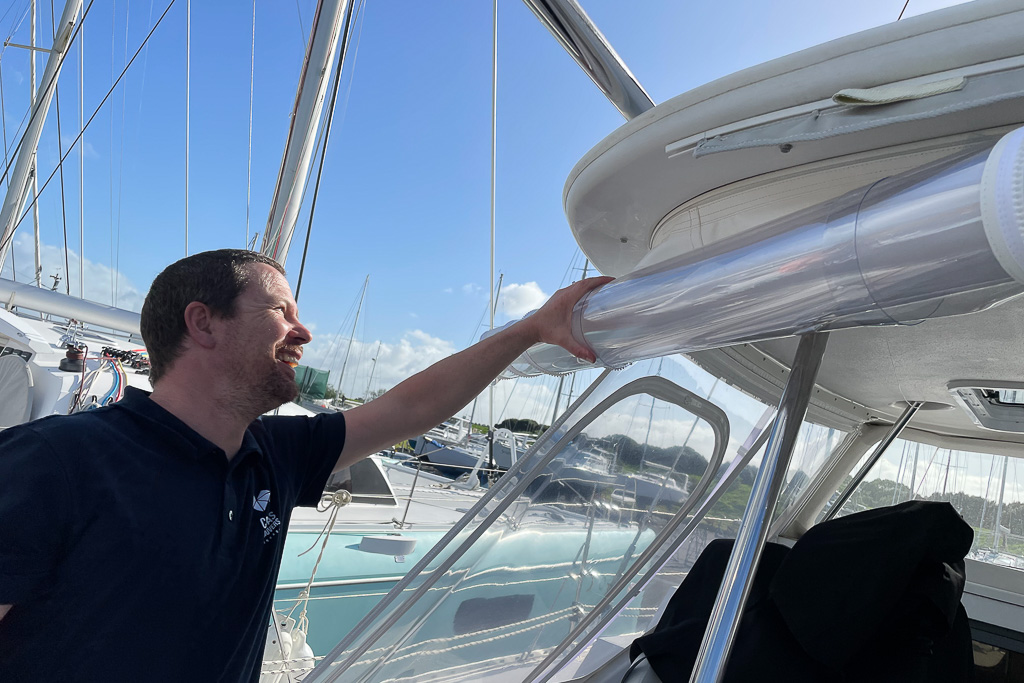
Exploring options for selling
We had been in touch with a boat broker in New Zealand when we entertained selling during COVID lockdowns but it seemed too difficult without returning to New Zealand to get the boat ready. He gave us an idea of where he thought the boat would sell, which was lower than comparables, especially with all the new equipment we had added recently. If listed, they would move the boat to Auckland and she would have to be boat-show ready. With all her offshore equipment and spares, it would be a big job to have her nearly emptied. If a Kiwi were to buy her, a 20% duty would have to be paid on her depreciated value, something we might have to eat. Not very appetizing.
We made a call to our friend and fellow Antares owner, Mark Silverstein, who now heads up marketing for new and pre-owned Antares Catamarans. It wasn’t practical for him to get involved in selling our boat due to her location but gave us some guidance on a listing price. He felt any listing would have to be on Yachtworld as she would most likely sell to an international buyer.
We then reached out to a guy from Vancouver who had contacted us last fall. Gerry had found us through the Bluewater Cruising Association directory. He was interested in buying a pre-owned Antares but didn’t want to buy a boat till around the fall of 2022. We advised him that we wanted to get on with selling the boat and didn’t want to wait till the fall. He requested and was sent a list on the updated equipment and inventory along with supporting documents. We showed him around the boat with a zoom call. He gave us an informal offer which we felt was in the ballpark, given comparables and her location. He agreed to fly down to New Zealand for a survey and sea trial.
Lifestyle
We were on week 5 or 6 of our stay in an AirBNB. It was located a short drive or bike ride from the marina. We often rode our folding bikes back and forth to get in a little exercise. A few weekend bookings by other guests were an inconvenience as we had to pack everything up and move to a motel.
Dining out was not enticing or easy as many restaurants were only offering limited menus and limited hours due to staff shortages. One brewpub with good pizzas about 25-minute drive from the marina shut down for several weeks.
We coped cooking on a 2-burner inefficient electric stovetop and a microwave. It would take 20 minutes to boil water. The fridge froze anything near the back. On occasion, we ordered take-out. A little store not far from the motel served the best fish ‘n chips. We tried the frozen dinners from the motel office a couple times. The lamb shank was the best.
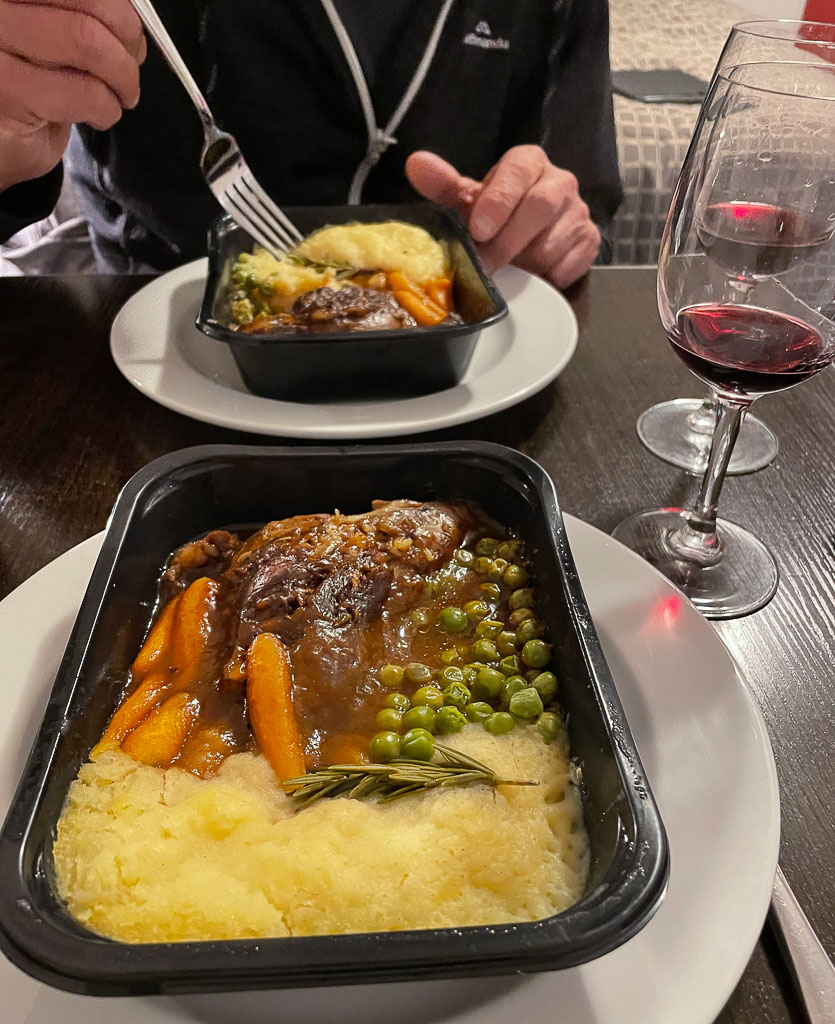
Moving on board made little sense with the strong possibility of selling. The temperature went down to 7 or 8 degrees at night, so our breath would have created condensation, making the boat damp. Sleeping on the boat in the boat yard in winter in New Zealand requires a de-humidifier. The one that our caretaker had kindly set up to keep our boat dry had to be returned to its owner. Buying one didn’t seem practical as it is large and hard to store. Another downside, the unheated boatyard washrooms and showers were a quarter mile walk from the boat.
Monty and the trades were constantly needing access to the lockers under the beds, couches and floorboards. Tools and boxes of equipment filled every corner and surface of the boat. Finding room for us and our luggage would have been challenging.
Our Personal Belongings
With selling more probable, we started to face the task of removing our personal belongings from the endless storage compartments on our boat. We had accumulated wheel-barrel loads of sports gear, clothing and sundry items over the five years. As Monty said, every year we would come down with six suitcases and go home with two! Stuff accumulated and with all the storage on the boat, we never seemed to run out of room for it. Antares are great for storage! We had to find a place to store what we took off. The owner of the AirBNB agreed to let us use his garage. What a godsend that was!
Decisions had be made quickly about what to try to sell, give away and bring home. Monty advertised some kites but only received brief interest from a few bottom feeders.
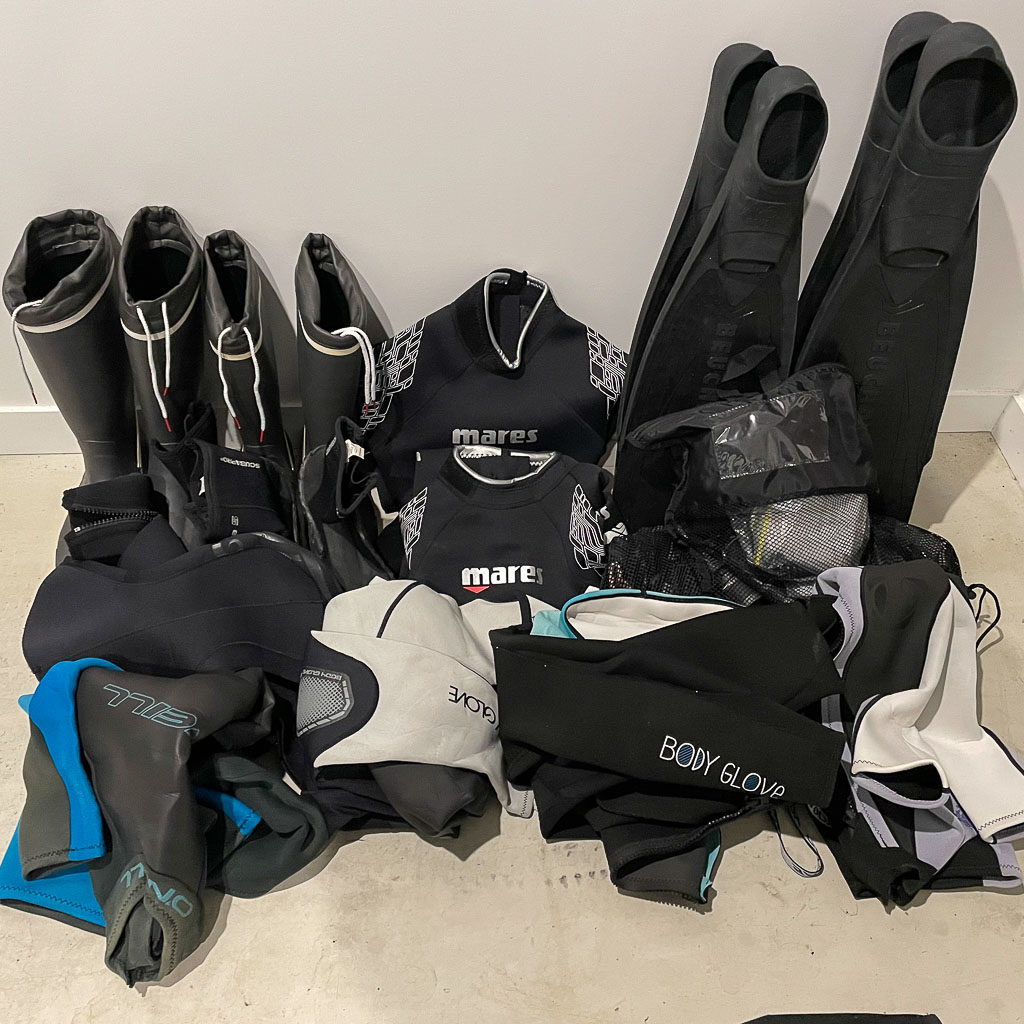
Out of Water Survey
Gerry, the prospective buyer, asked to have an out of water survey done while the boat was still on the hardstand. Most surveyors we contacted were not available until the end of June and one had just come down with Covid. Jon Jones was engaged to do the survey for Gerry the day before Whistler was to splash. He took photos, inspected the exterior, tapped the hulls and tested the moisture in the hulls with a special device. The hulls had no issues but he did notice some dried mud from mason wasps (aka mason bees) in the small anti-syphon through-hulls. These wasps are native to New Zealand. Monty scraped out the nest debris to prevent a blockage when the engines were started. He also pointed out a corroded zinc inside one rudder post which Monty quickly replaced.
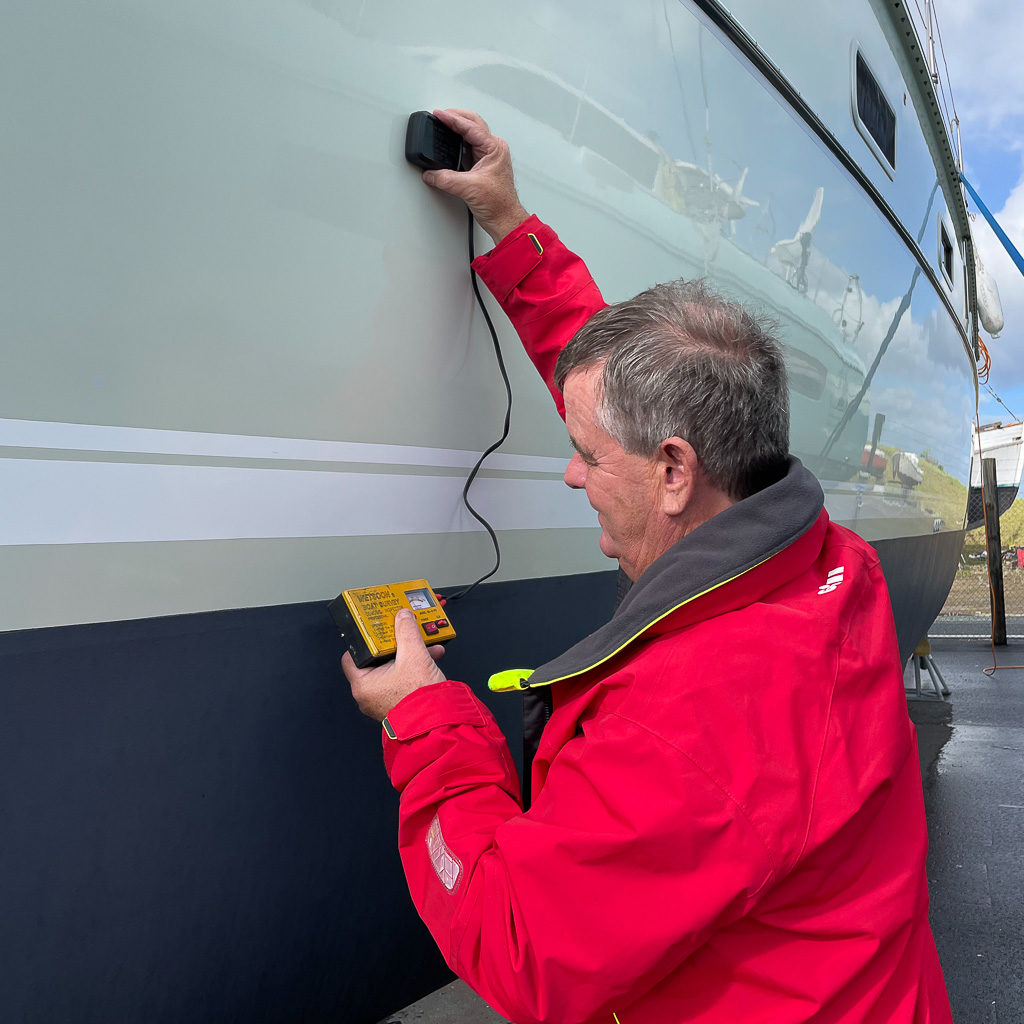
Splash Date
After a six-week maintenance program on the hardstand, Whistler was finally ready to go back in the water. The haul-out team had an opening in their busy schedule. She was lifted onto the trailer on Wednesday, June 15th.
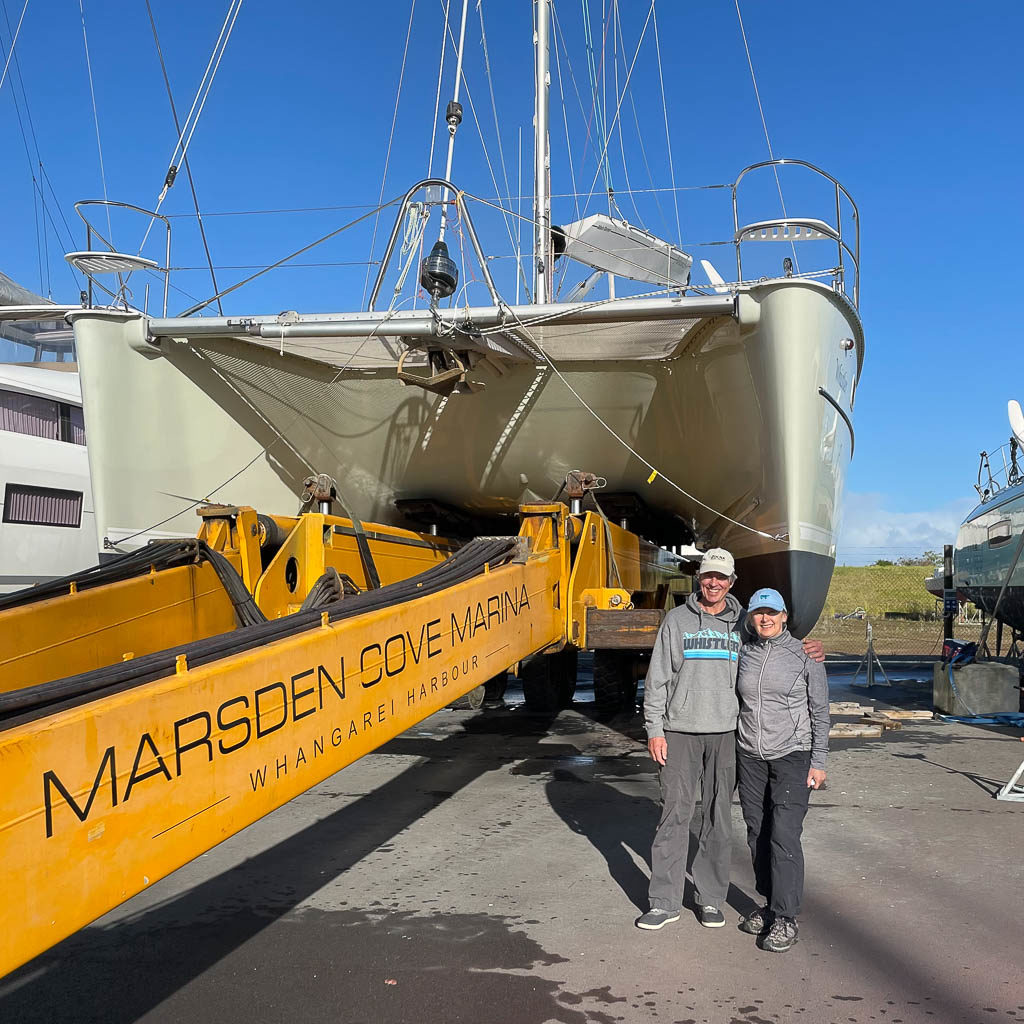
I walked around the boat late that afternoon and noticed the copper bolts on the grounding plate for the single side band radio were badly corroded. Could the plate fall off or a leak develop?
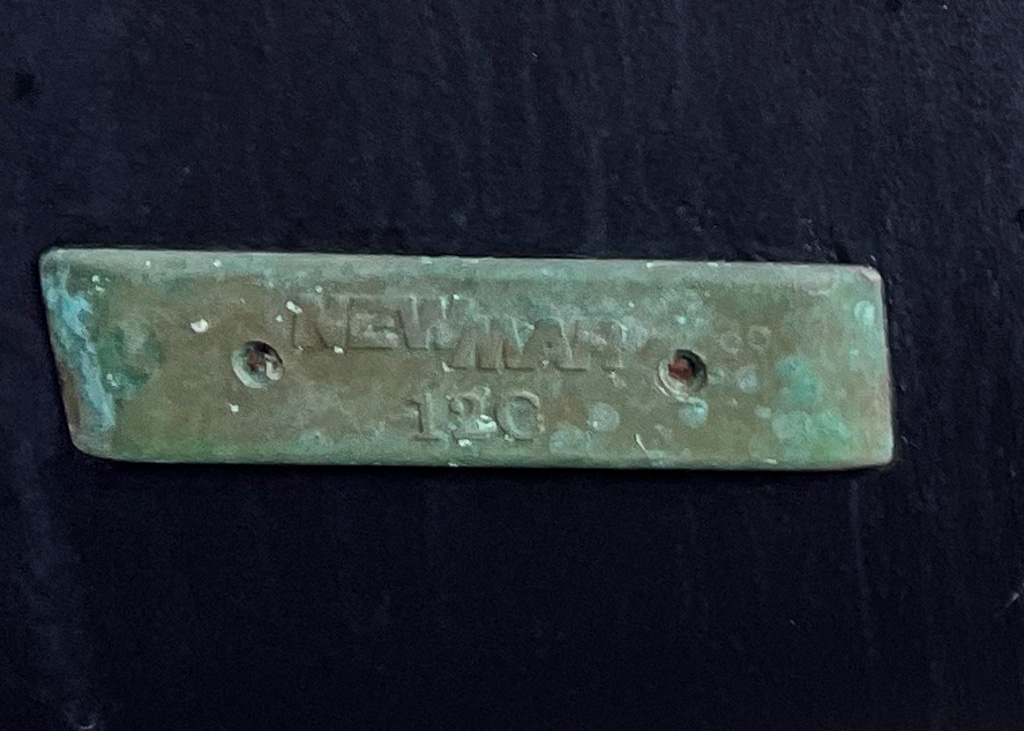
We were glad we noticed it before launching. It definitely had to be fixed before the launch the next morning! Monty and Larry worked quickly to remove and replace the corroded bolts and seal them up with Fix 15 Adhesive Sealant.
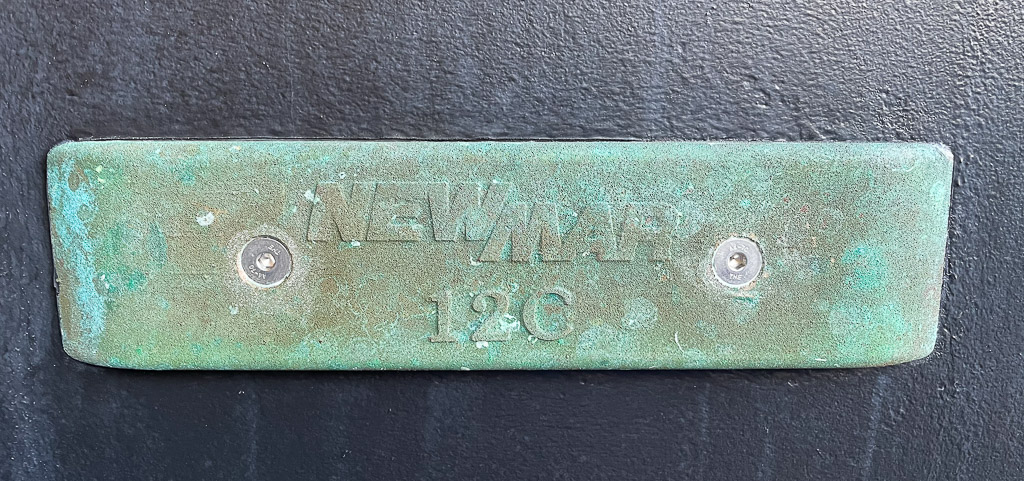
We were grateful that the morning of the launch was a beautiful calm day. The moon was just dropping in the sky as I took this photo of the yard.
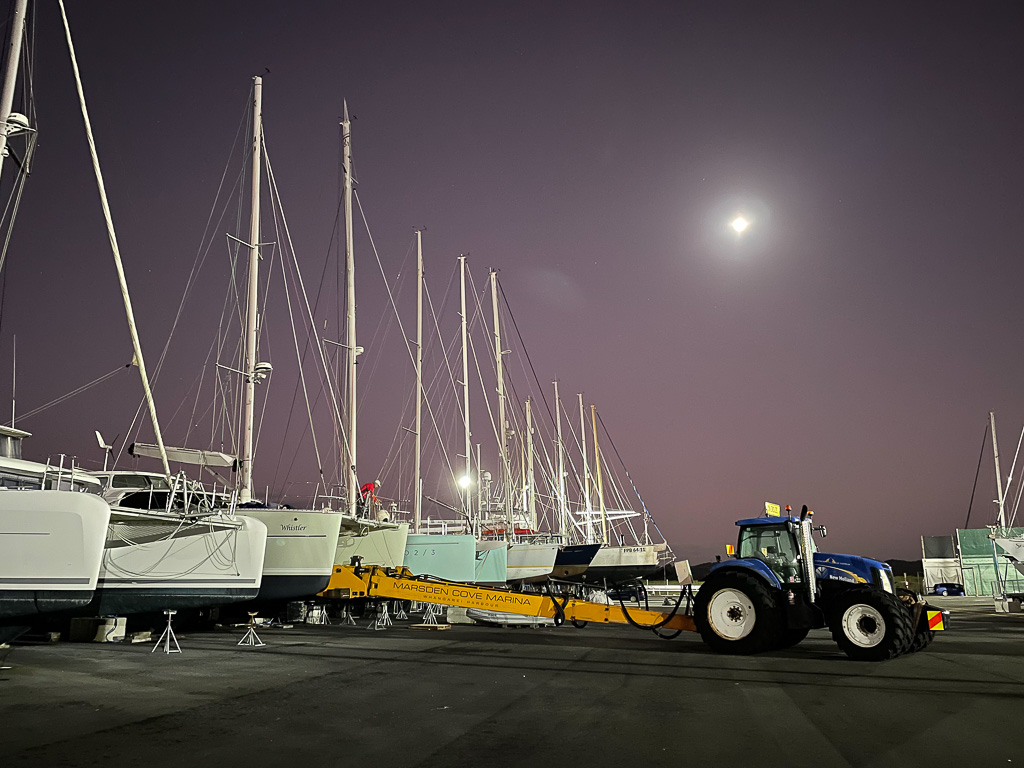
Monty secured the fenders.
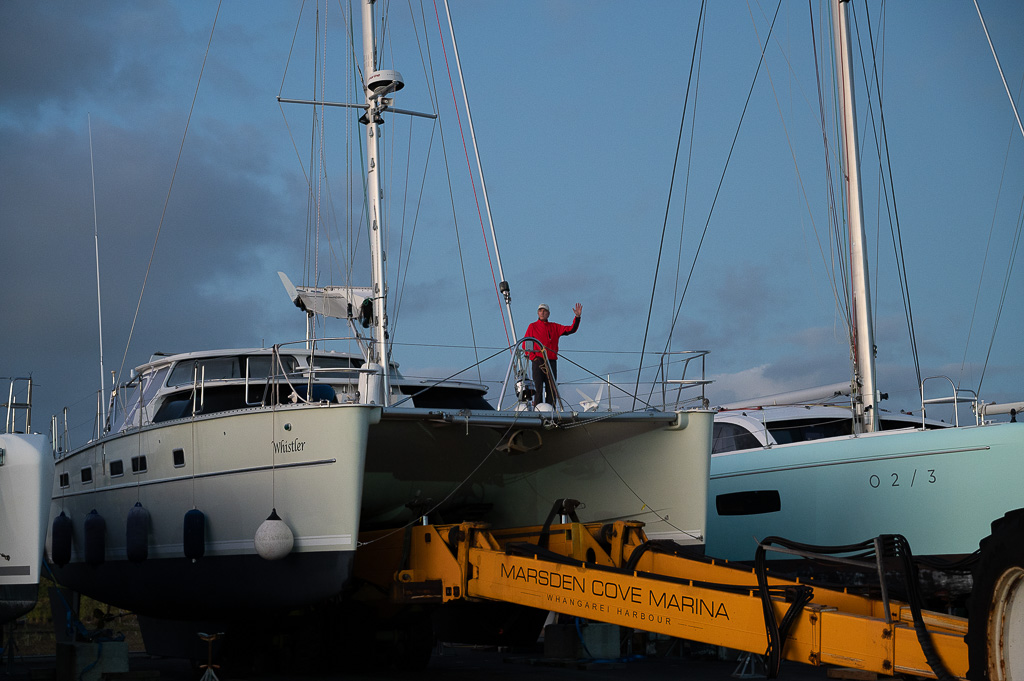
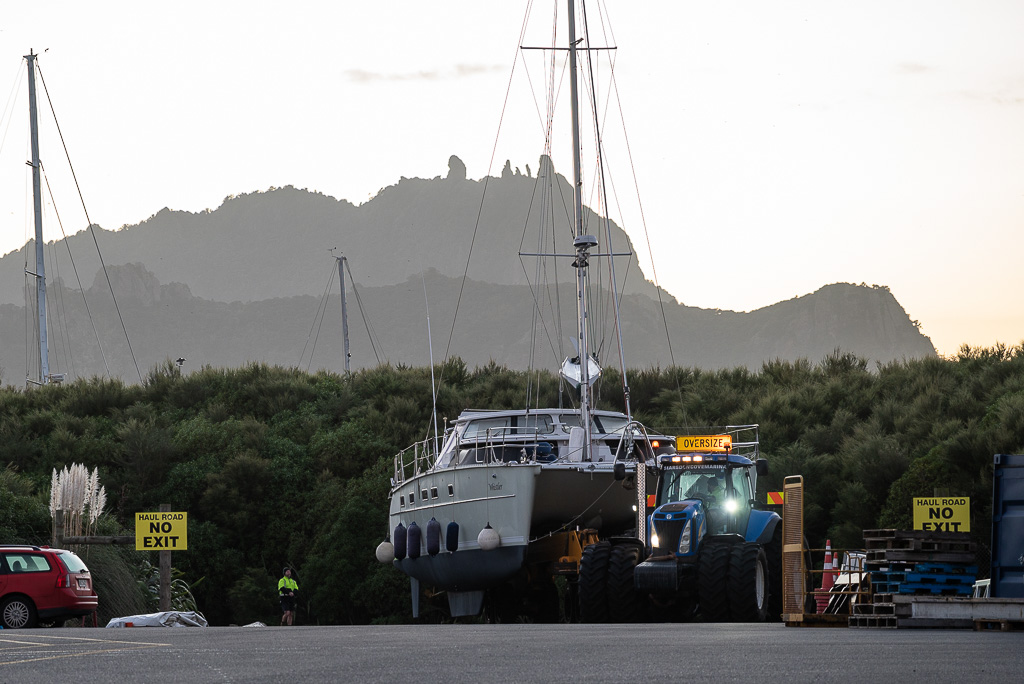
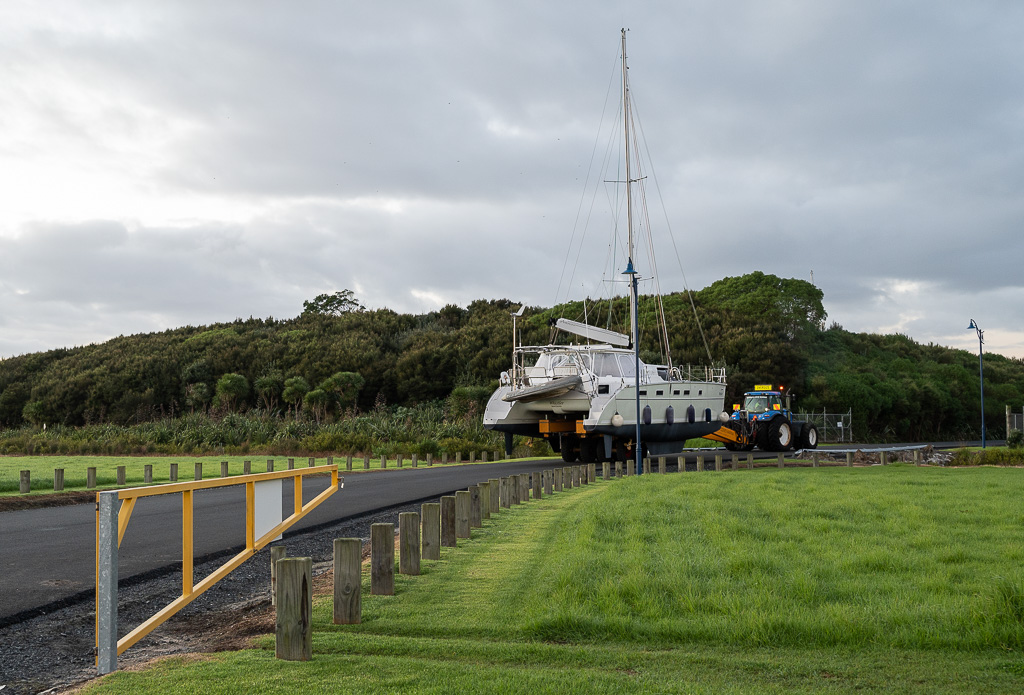
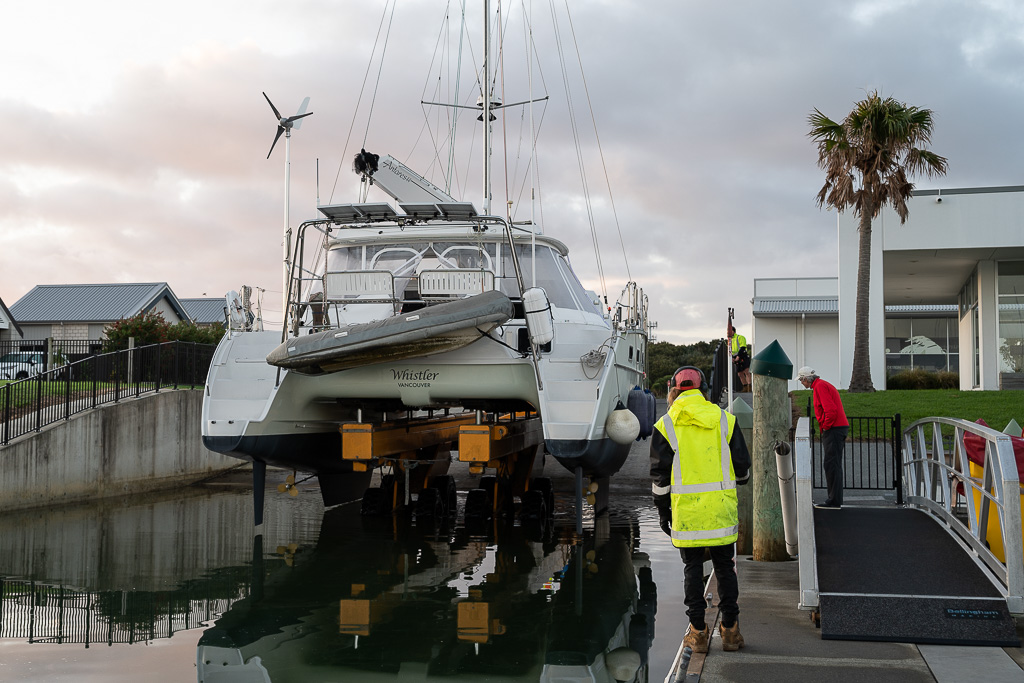
Final Mechanical Maintenance
As soon as Whistler was floating, the mechanic and his apprentice arrived to finish their maintenance on the generator. The two engines, generator and three air conditioning units all started up without any hesitation. Once the boat was docked in her slip, the serviced outboard was delivered and mounted on our dinghy. The electric-start Yamaha engine started up and “purred”. We highly recommend Brendon and his team at Marsden Cove Marine Services.
Sails and other deliveries
Craig, our sailmaker from Willis Sails drove down from Kerikeri on Friday with our main, genoa and screecher sails. He had kindly been storing them in his loft during COVID.
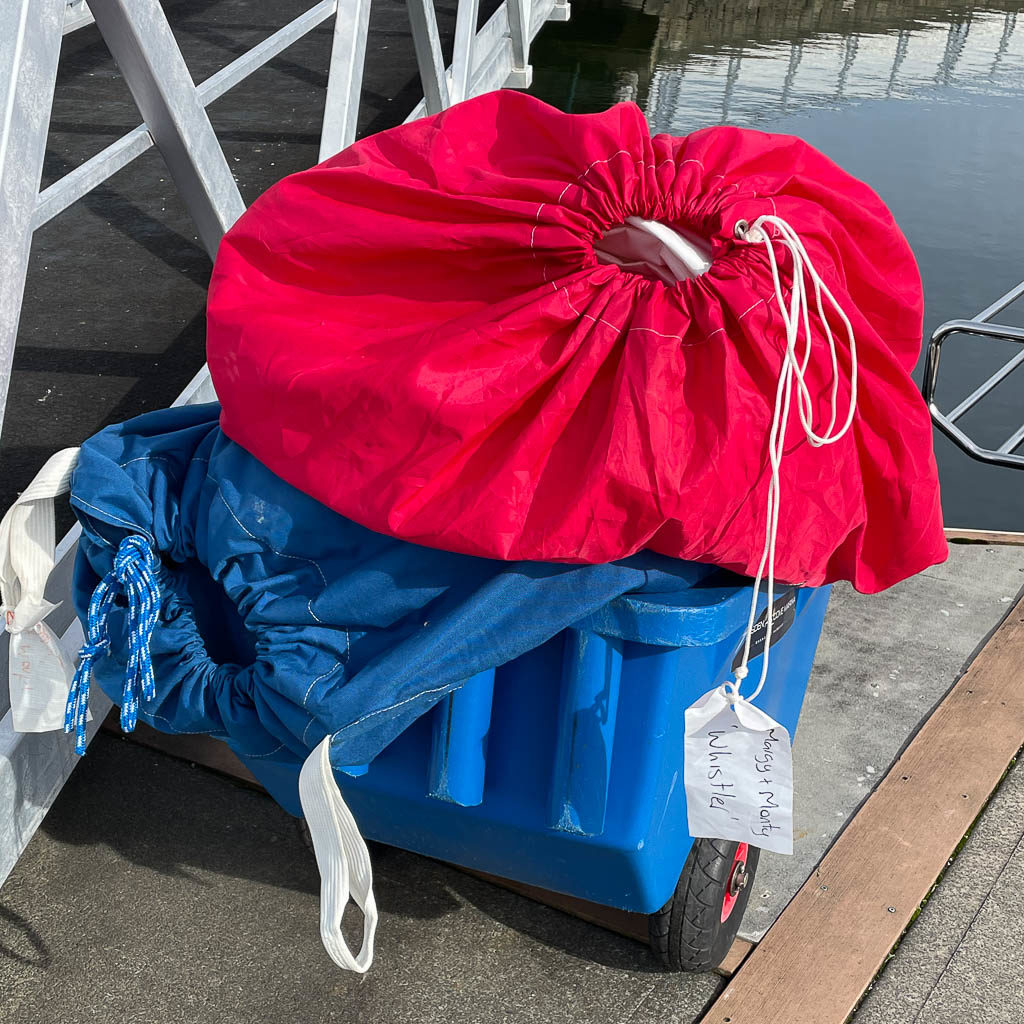
It was a perfectly calm day for putting the main back on. Craig had even remembered to add the “i” to the “Antares 44” on the sail.
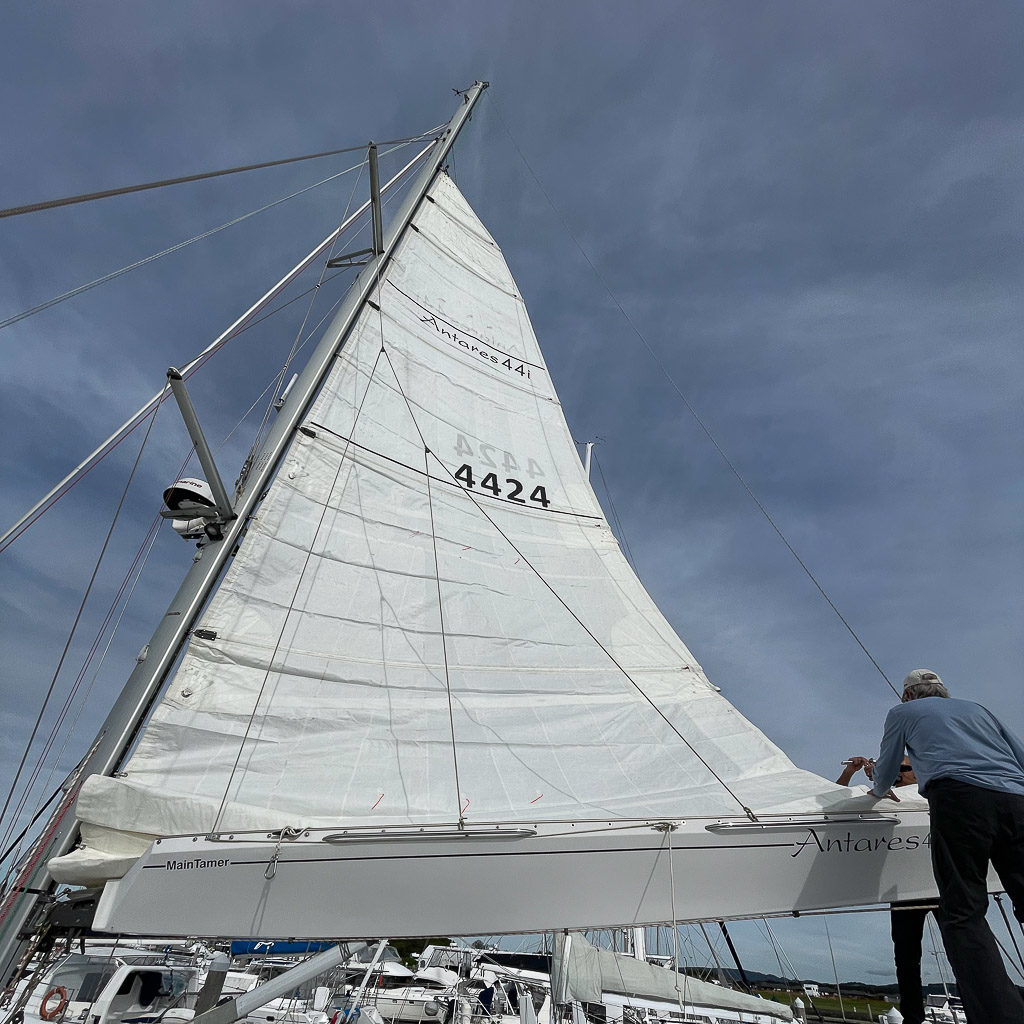
Monty made an unfortunate finding when the main was being raised. The skeletal remains of a dead bird and its abundant nesting material was lodged the inside of the boom. It had gotten trapped making a nest, despite Monty’s and our caretaker’s efforts to prevent such intrusions by netting the front and back ends of the boom. It was a chore to pull out all the twigs and get the reef lines freed up.
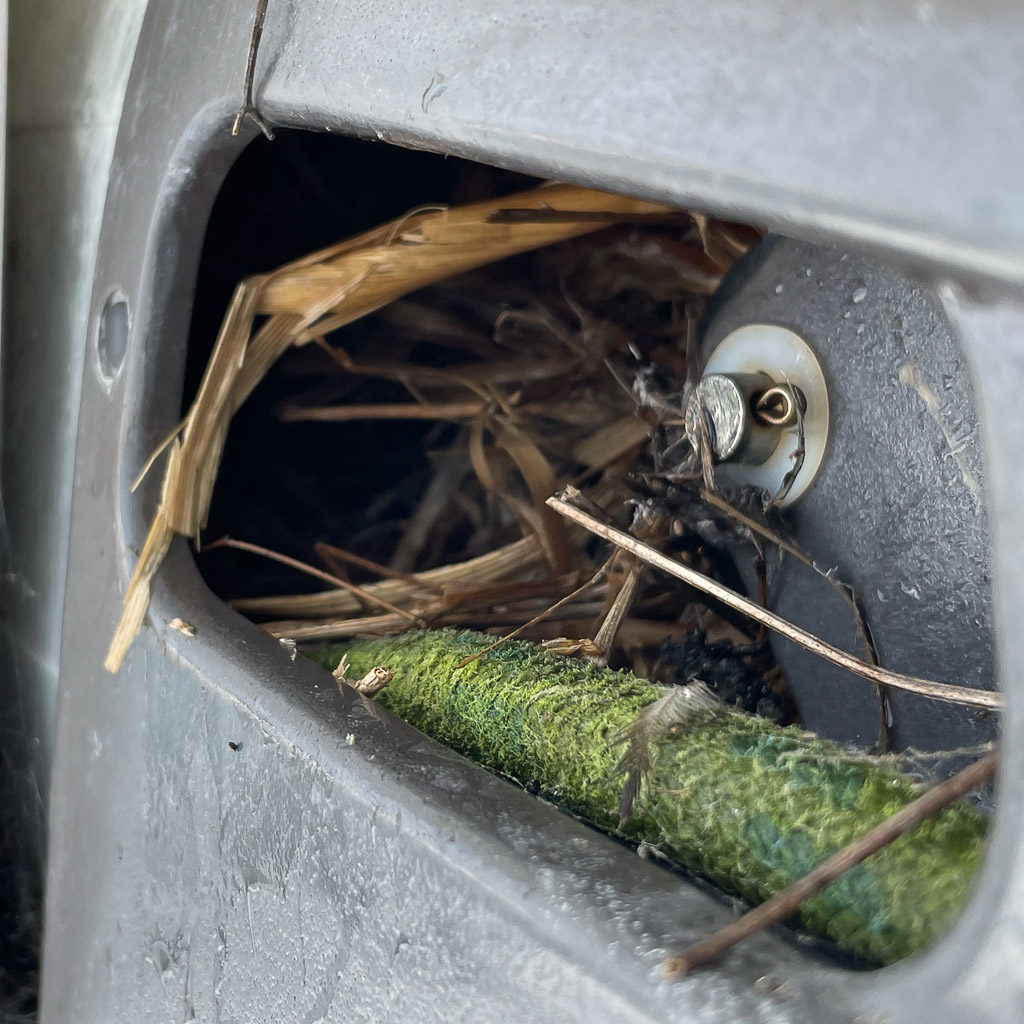
The main and genoa were like new. Craig drove down from Kerikeri and took off the mainsail when New Zealand locked down.
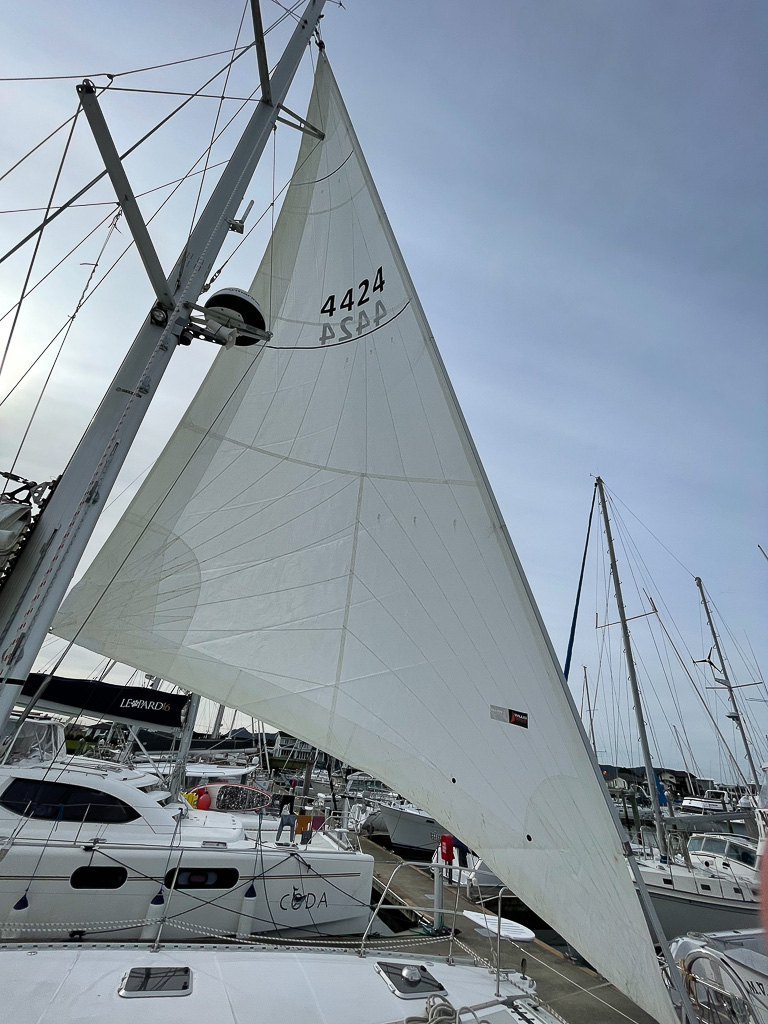
The new screecher with laminate fabric was raised. We didn’t leave it up long but it looked beautiful. Why are we selling again?
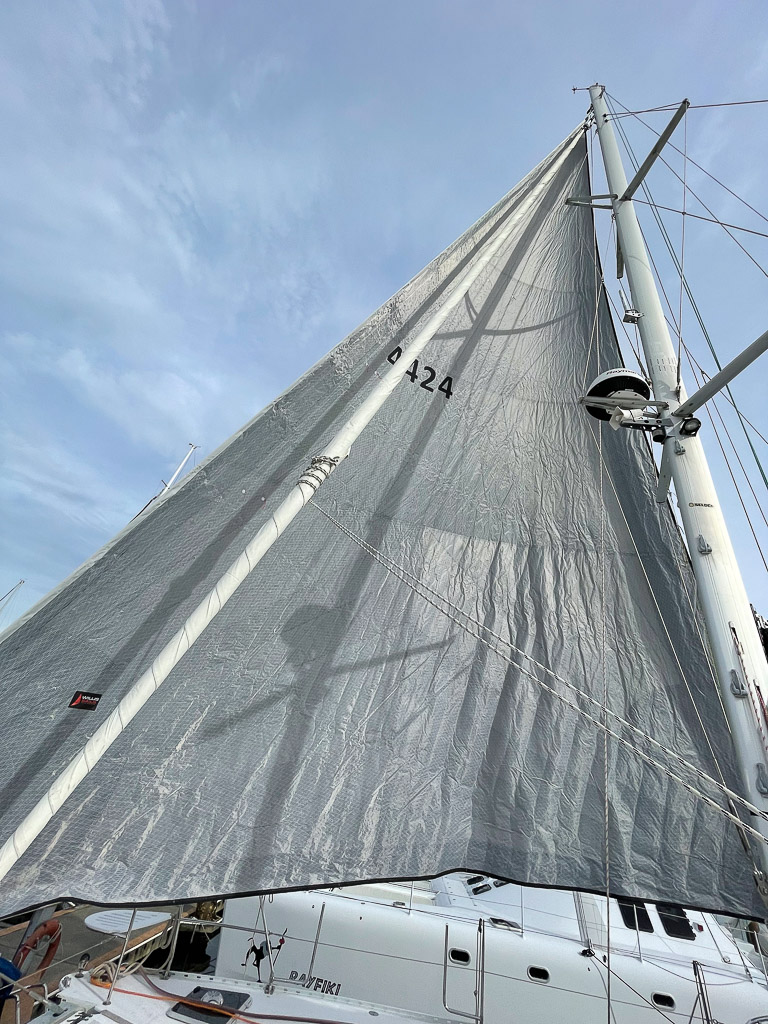
Getting a new mesh window screen was an exercise in patience. Canvas & Covers came a few times to measure, the last time with a new laser device. When Brendan came to install the new screen, it didn’t fit. The fittings had been put on the reverse side. They had to build a new one from scratch. About two months after being ordered, they delivered it. It looked very good, made with some French fabric that is guaranteed for ten years.
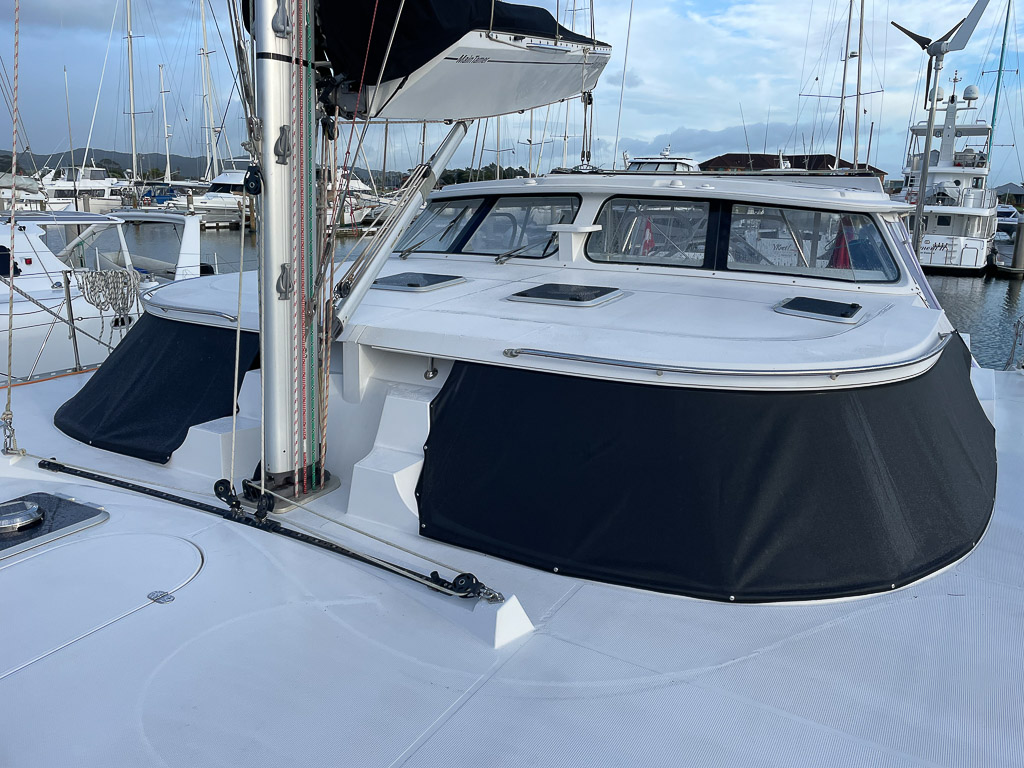
Gerry Arrives
The prospective buyer arrived after a gruelling 4-flight journey from Vancouver through LAX, Tahiti and Auckland. We picked Gerry up from the Whangarei airport and did a brief tour of the town on our way out to Marsden Cove. We did a brief tour around the boat. He remarked how good the boat looked for its age. He asked: “How do you keep the decks so white?”
Monty took him for a ride around the marina in the dinghy. It was staying well-inflated since its visit to the dinghy doctor, Northland Inflatables.
In-Water Survey
Two days of high winds and rain delayed the in-water survey. The surveyor did his inspection on Wednesday. Nothing significant was found to deter Gerry but the surveyor made a few helpful suggestions.
Sea Trial
The sea trial was conducted on Thursday, June 23rd. We picked a day with light winds, making it easy to depart and return to our slip in the marina. Outside the mouth of the river, winds picked up to 18 knots. We raised the main and put in a reef. The genoa was unfurled and then a reef was put in it too. Whistler sailed beautifully at 8 knots. I looked at Monty and asked: “Are you sure you want to sell?” We turned around so we could reduce the apparent wind, furled the genoa and unfurled the new screecher.
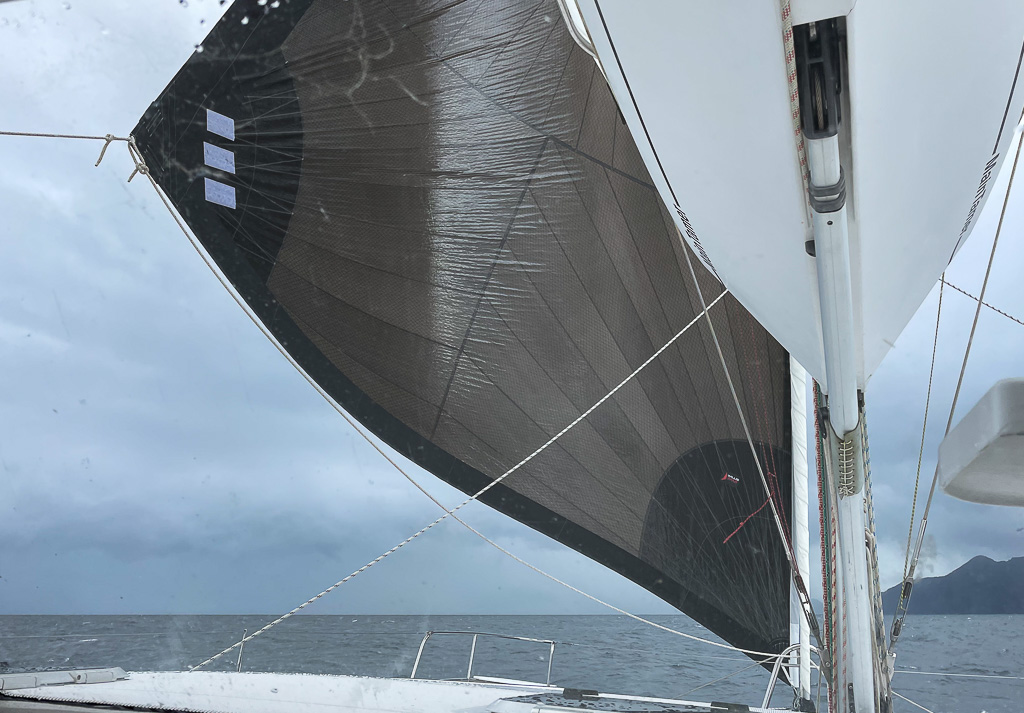
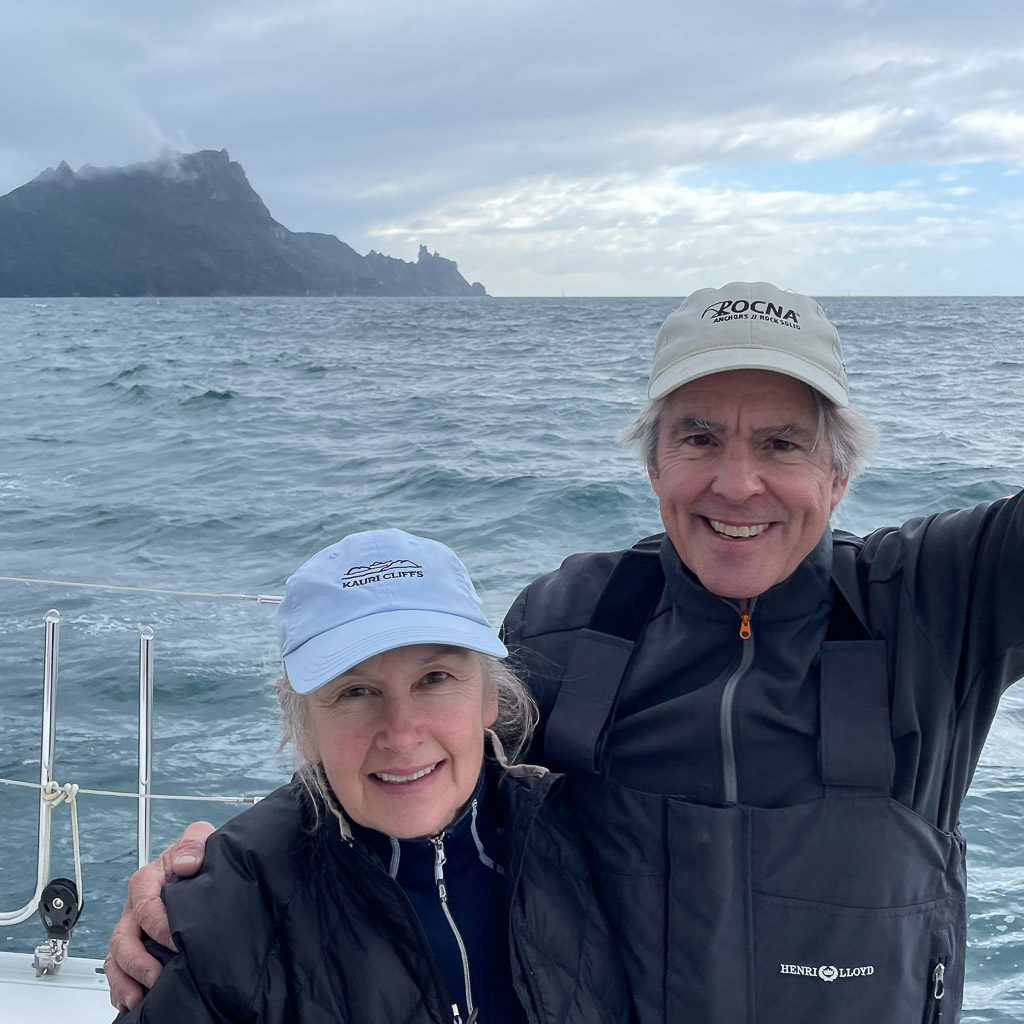
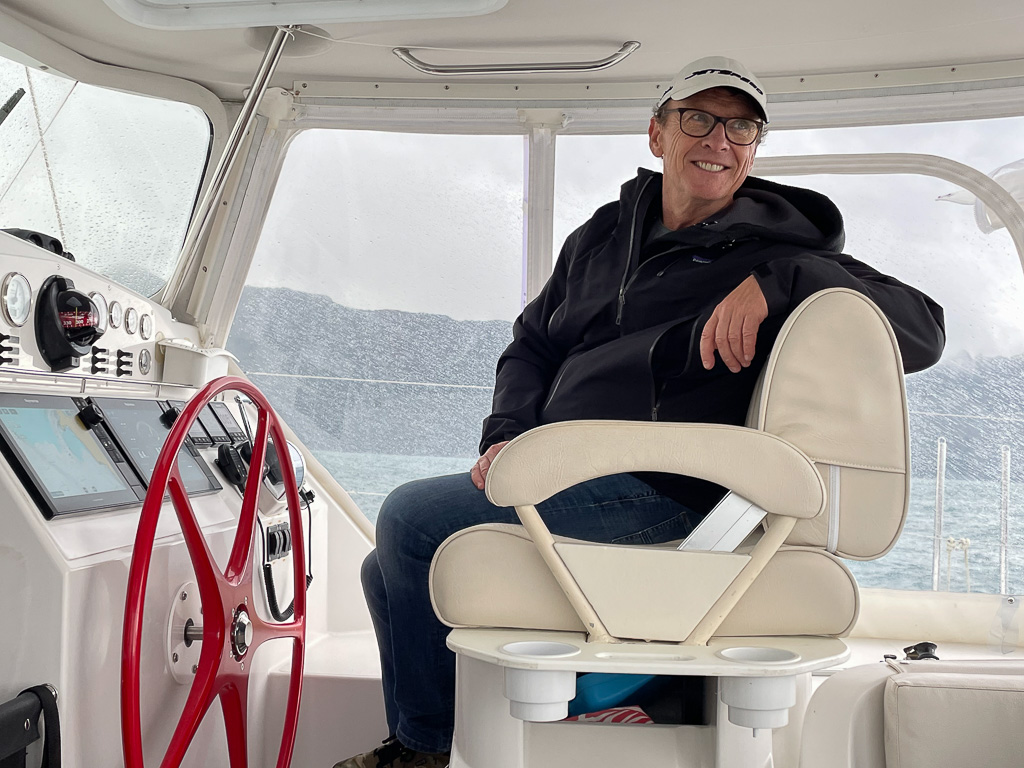
We motored into Urquharts Bay to show Gerry how to anchor the boat and put the bridal on. He and Monty got soaked by a downpour. We recalled when Christian, the previous owner, had done the same for us in 2015.
Since we left the boat in November, 2019, the watermaker had been programmed to flush every 5 days. It carried on doing its automatic flushing on schedule for 30 months. Monty had changed the filters but wanted to run it since we were out of the marina. It ran to “spec”, making 50L (12 1/2 gallons) per hour! Monty let Gerry know not to expect that production in the tropics where the water is warmer.
Decision Time
Gerry had been quiet and a bit difficult to read. At the end of the sea trial, we asked him if he was going to buy the boat. He said “yes“, recounting he had always intended to buy her. He started finalizing the paperwork with a law firm in Auckland and arranging the transfer of the funds. The maritime lawyer who helped us with the purchase reviewed the documents on our behalf.
Logistics to Get Home
Moving our flights home from November to July and getting our luggage ready and shipped became the next priority. Flights were very booked up. We had to spend 3 hours on hold every time we called Air New Zealand. We finally decided to pay up to fly home on July 6th, the same day that Gerry was flying back to Vancouver.
I contracted COVID but neither Monty or Gerry ever got it. They had both had Covid in December/January. I isolated and we all tested almost daily. Once I felt up to it, I attacked the piles of clothes and sports gear, setting aside items to give away and pack to bring home. I researched shipping excess luggage and decided air cargo was the way to go. When I was over COVID, we drove to Auckland and dropped off our baggage with Air New Zealand Cargo. We were happy knowing it was going on a direct flight to Vancouver.
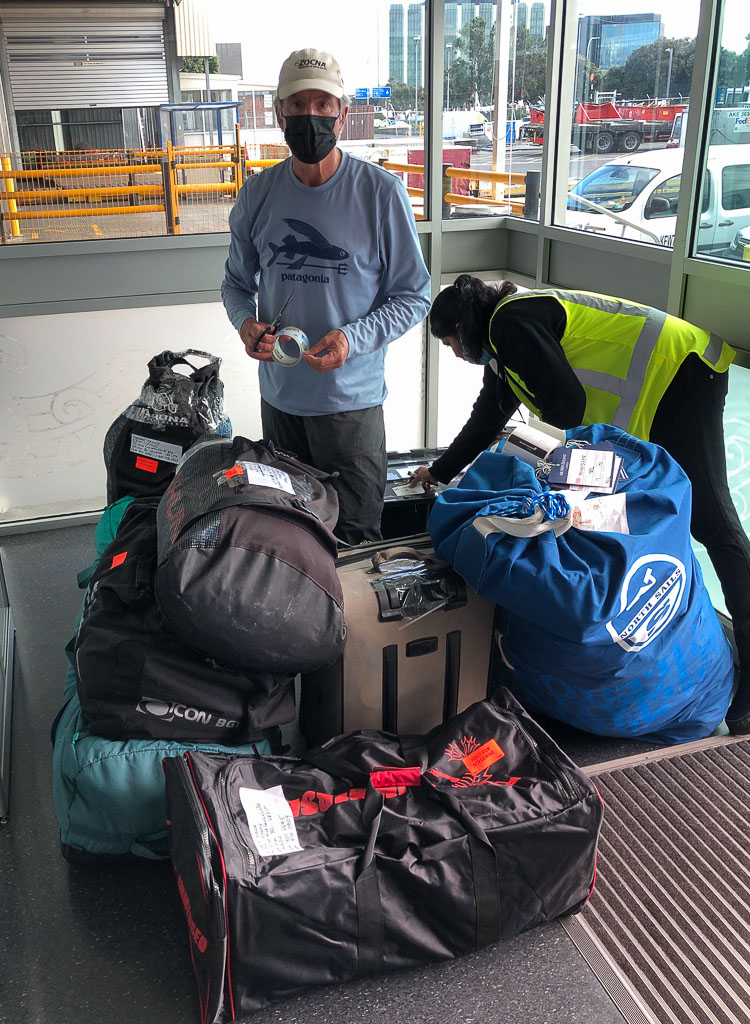
Gerry’s Orientation to Whistler
Monty and Gerry spent about ten days going through the boat systems and inventory of tools and spares, locker by locker, box by box. Gerry took notes and photos. They ticked off the items on the comprehensive list created by Christian, the previous owner, for our purchase.
We said our good-byes to the boat with some tears and wished Gerry well.
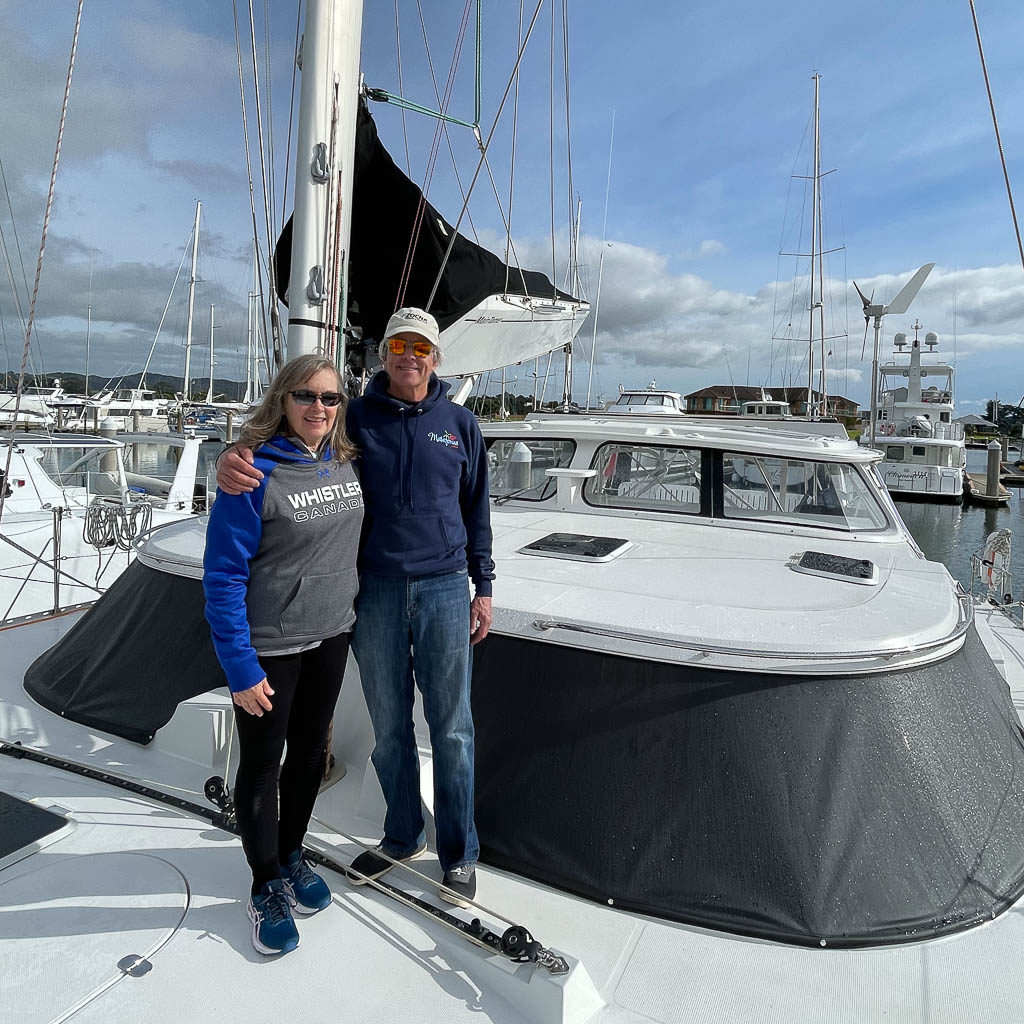
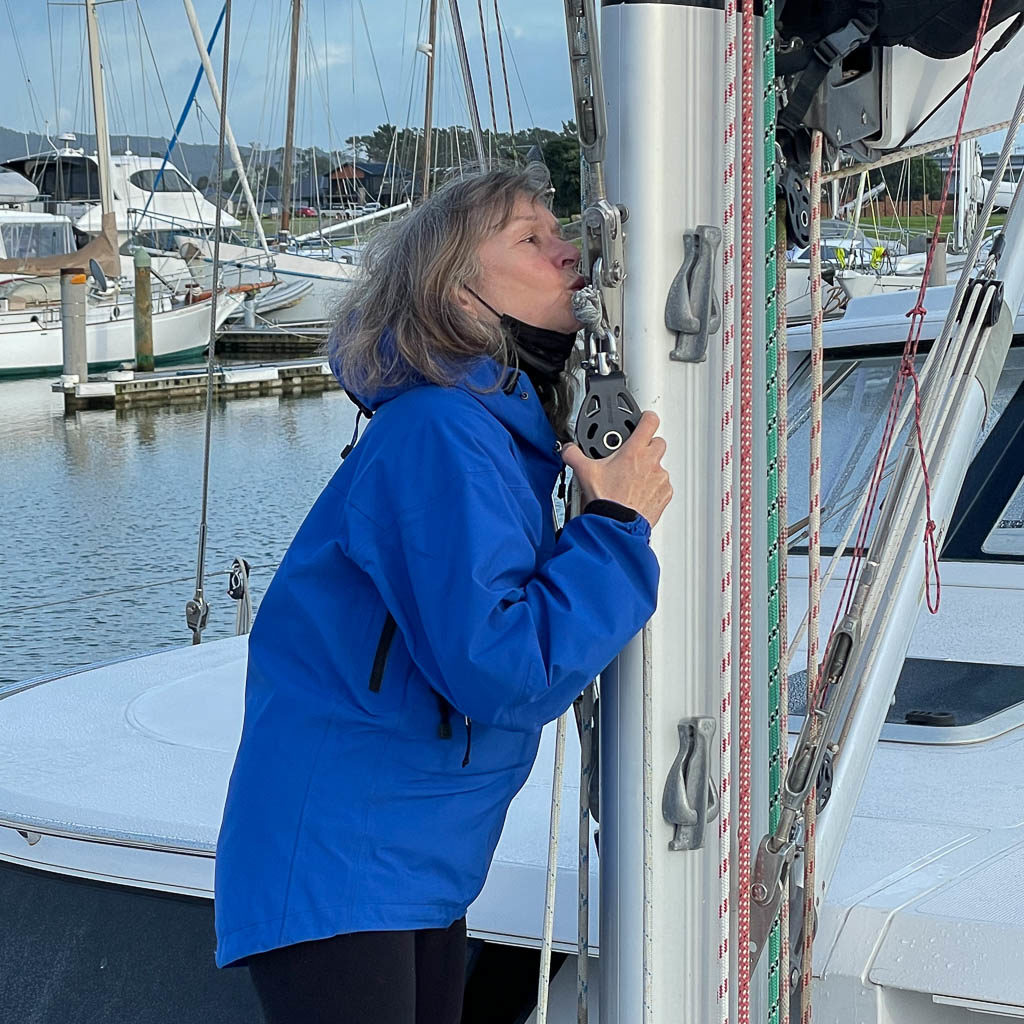
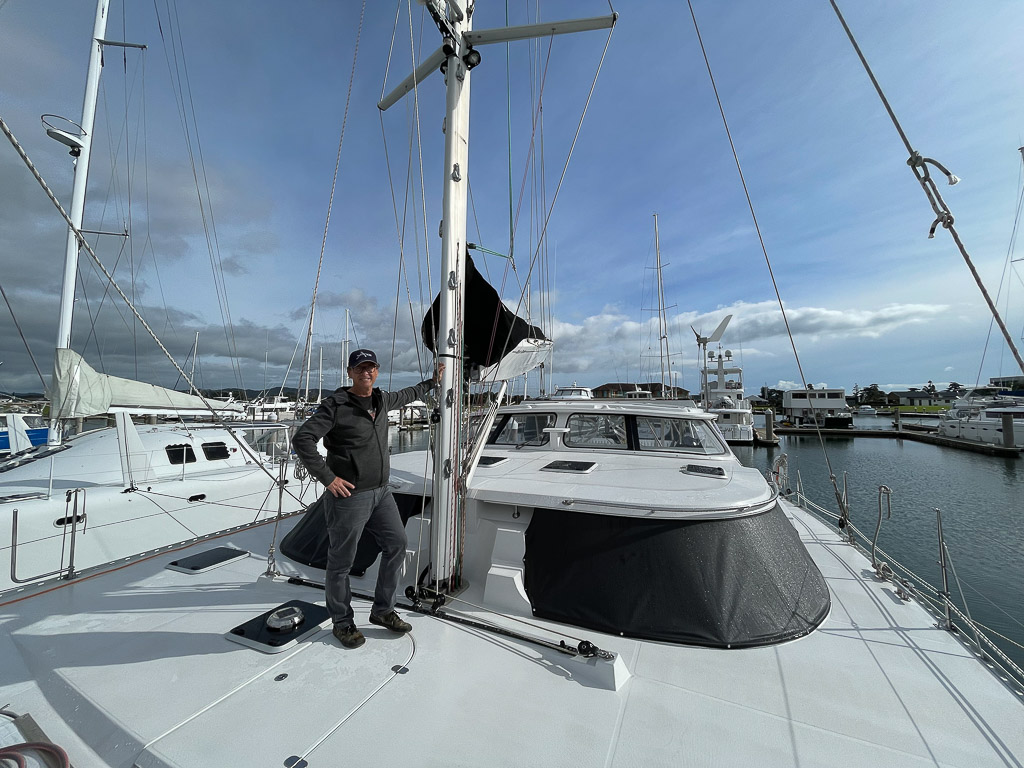
Back Home
Monty has been keeping my spirits up by looking at “boat porn“, the expression for scanning YachtWorld listings. The boat market has been very hot but there are signs it is slowing. Finding moorage is extremely difficult with multi-year waits for a good location. We viewed a few boats in Vancouver and Victoria but none “spoke to us“. When and where we might buy another boat, or if it will be sail or power, but we will update you if we do! The urge to explore the Pacific Northwest and Alaska still lingers.
Reflections
Whistler was the perfect offshore catamaran, manageable for a couple, comfortable, safe and well-built. We want to thank the Antares family and designer, Ted Clements, for their invaluable support. We know Gerry is in good hands.
A highlight of our time on Whistler was meeting so many interesting, inspiring and generous cruisers and a few resort owners in Tonga and Fiji. We hope to stay in touch and retain many of these friendships. We will follow our cruising friends as their journeys continue and Whistler X as she embarks on her next chapter with Gerry.
Cruising has been an unforgettable adventure. In addition to honing our boating skills, we learned to kite board and scuba dive. As a photographer, it was a delight to have so many spectacular marine vistas to shoot. Tasting the Polynesian culture and being welcomed by the smiling Fijians was special.
We hope you have enjoyed coming along with us as we experienced the magical cruising life in the South Pacific.
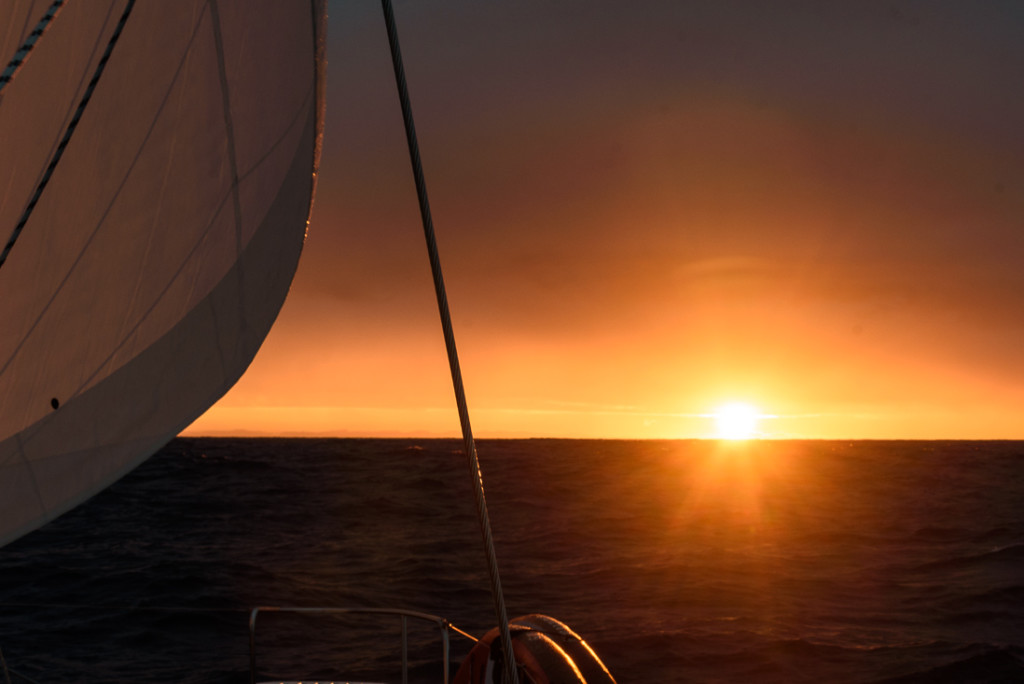
10 comments
What an end to a wonderful chapter! Glad we were there when it started…all the best on life’s next adventure for you both!
Thanks, Beth! Hope all is well!
Thank you for sharing ! It’s been challenging times for many! I look forward to your next adventure! H & K. Rachelle
The end of a very interesting chapter of your lives and moving onto new adventures! Best wishes, Jacquie
Thanks, Jacquie! Please let me know when you are out our way!
Thank you for sharing with talent and great pics your final adventure with Whistler.
Songhui and I read it rabidly, including boot of “boat porn”, what to do with the sports gear and the incredible effort to prepare the sale. It was also for us a long story.
We are now getting reacclimated to New York. We dedicated early 2022 to renovate our Guest bed-room …and we are happy to extend an invitation when you will be around.
We joined One 15 Sailing Club (J80 and Melges 24). In order to be skipper and “certified” to take a club boat with friends, I had to jump so many hoops and specific training. Ironically
I had zero “permit” to buy a boat and sail it half the world around safely.
Finally to put all this in perspective:
– we are aging but in good spirit
– Songhui is getting promoted
– We all know that to get rescued after a Mayday in the Central Atlantique, it will take 3 to 4 days, in the Pacific 4 to 6 days, but in New York 5 to 10 min….
We will love to have you and/or talk to you !
Cheers
Songhui & Dominique
likely is a couple of days
neraly around the worlddethe whim of the Commodore
if you are around.
,
il.
equipement.
and “boat porn” the sports .
ing ra- with gre
Hey Monty and Margy
We understand how sad you feel but there is life after cruising or you can find other avenues to enjoy the cruising life as we have done since selling Sally. The new owner is very lucky as he has a very beautiful boat.
We do hope maybe one day our paths with cross. We often reminisce about our time spent with you in the islands especially some of our kiting adventures.
XXX
Margy,
What a wonderful commentary on a fabulous adventure! I really enjoyed reading this – thanks for sending.
Cant wait for your next adventure!
I am completely exhausted after having read your Blog. Perhaps you should buy a Benneteau in the Caribbean. At least it is warm there year round. Have a great summer. If you are passing through Toronto, give a call. Cheers Noreen.
Oh well, it had to come at some point. We’re glad to have had a small opportunity to intersect with you two in Whangeri some years ago. Diane and I are still in Turkey, and enjoying it here. Next year, or maybe the year after – we will push on West to Tunisia and then eventually to the Caribbean. We enjoyed our time in the South Pacific, as you obviously did as well. Best of luck in your new endeavours.